Friday, November 22, 2024
How to Build a Wood Pallet Shed: Easy Plans for a Stylish Outdoor Shed
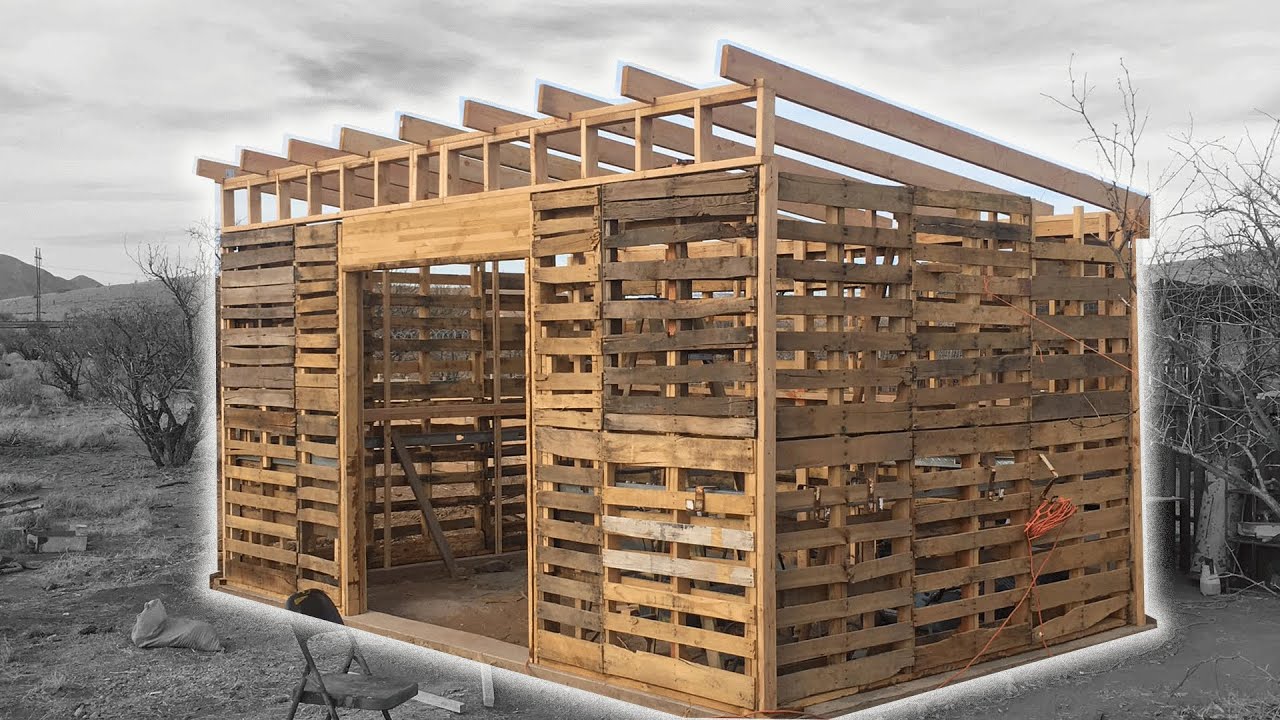
How to Build a Wood Pallet Shed: Easy Plans for a Stylish Outdoor Shed
Hey there, fellow DIY enthusiasts! So you're dreaming of a charming little shed, perfect for storing garden tools, bikes, or maybe even a cozy reading nook? And you're thinking of using reclaimed wood pallets? Fantastic! It's a super eco-friendly and budget-friendly option, plus you can get a really unique, rustic look. Let's dive into building your own pallet shed! Don't worry, even if you're a beginner, this project is totally doable.1. Planning Your Pallet Shed Paradise
Before you even think about grabbing a hammer, we need a plan. This isn't rocket science, but a little forethought saves a lot of headaches later on.1.1 Size and Location
First things first: how big do you want your shed to be? Consider what you'll be storing. A small shed for tools is different from a larger one that might house bikes and gardening supplies. Measure the space where you plan to place it, ensuring you have enough room to open doors and work comfortably. Also, think about sunlight â" do you need a sunny spot or a shadier area? Check local building codes for any restrictions on shed size or placement.
1.2 Pallet Selection: The Treasure Hunt
Now for the fun part â" sourcing your pallets! You can often find free or cheap pallets behind businesses, on Craigslist, or even Facebook Marketplace. Important note: Inspect them carefully! Make sure they're sturdy, free of rot, and haven't been treated with harmful chemicals. Look for the HT stamp (heat-treated) â" it means they're safe to use. You'll need quite a few, depending on the size of your shed, so start your hunt early.
1.3 Tools and Materials
Gather your arsenal! You'll need:
- Measuring tape and level
- Hammer or nail gun
- Screws (exterior-grade are best)
- Wood glue
- Saw (circular saw or hand saw)
- Safety glasses and work gloves
- Post hole diggers (if you plan on a concrete base)
- Concrete mix (optional, for a more stable base)
- Optional: Pressure treated lumber for the base framing if you are not using a concrete base
- Optional: Roofing felt and shingles
- Optional: Paint or stain for a finished look
Remember to always prioritize safety! Wear safety glasses and work gloves throughout the project.
2. Building the Foundation: A Solid Start
A sturdy foundation is key! You have a couple of options:
2.1 Concrete Base
This is the most permanent and robust option. Dig holes for your base supports, pour in concrete, and let it cure completely. Once set, you can attach your base framing to the concrete using anchors.
2.2 Wooden Base
A simpler approach is using pressure treated lumber to construct a frame. This creates a raised base and keeps the pallets off the ground, preventing rot. Ensure this base is level before continuing.
3. Constructing the Walls: Pallet Power!
This is where the pallet magic happens. Clean your pallets thoroughly, removing any loose nails or debris.
3.1 Wall Assembly
You can build walls either by stacking pallets directly or by creating a frame and attaching the pallets to it. For a more robust structure, using a frame is recommended. Build your frame using pressure-treated lumber and attach the pallets to this framework using screws. Consider using more than one pallet to build a taller wall section if needed. Work in sections until the walls are complete.
3.2 Securing the Walls
Once your walls are assembled, connect them using additional framing and screws to create a sturdy rectangular structure. Ensure the corners are square and properly aligned. You might want to use bracing inside the structure to add extra support.
4. Roofing the Shed: Shelter from the Storm
Now for the roof! There are several options here, depending on your skill level and desired aesthetic:
4.1 Simple Shed Roof
A single-sloped roof is easiest to build. You'll need to cut some pallets to the right size and angle for the roof and secure them to the top of your walls.
4.2 Gable Roof
A gable roof (with two slopes meeting at a ridge) offers more headroom inside, but is slightly more complex to construct. You will need extra supports and more precise cuts for this option.
4.3 Roofing Material
Once the roof structure is complete, you can add roofing felt to make it waterproof and then add your shingles or other roofing material of choice. Remember to overlap the roofing material to ensure complete protection from the elements.
5. Finishing Touches: The Personalization Phase
This is where your creativity shines! You can:
- Paint or stain the pallets for a more polished look.
- Add a door (a repurposed door works wonders).
- Install windows for ventilation and light.
- Add some landscaping around your new shed to make it blend seamlessly into your garden.
Commonly Asked Questions
Q: How long does it take to build a pallet shed?
A: This depends on the size and complexity. Expect to spend several days to a couple of weeks, depending on your experience and how much time you can dedicate to the project.
Q: Are pallets always free?
A: Not always. While you can often find free pallets, some may charge a small fee. Be sure to inspect pallets for safety and structural integrity before using them.
Q: What kind of paint should I use on pallets?
A: Use exterior-grade paint designed to withstand the elements. Apply multiple coats for better protection.
Q: Do I need planning permission to build a shed?
A: It depends on your local regulations and the size of the shed. Check with your local council before starting your project.
Q: Can I use any type of pallet?
A: No, it's important to only use pallets marked "HT" (heat treated) as these are safe for use. Avoid using pallets treated with chemical pesticides, as these are unsafe and potentially dangerous.
There you have it! Building a pallet shed is a rewarding project that combines creativity, resourcefulness, and a touch of rustic charm. So get out there, find those pallets, and unleash your inner builder. Happy shedding!
Thursday, November 21, 2024
The Ultimate DIY Lean-To Shed: Step-by-Step Plans for Outdoor Bliss
The Ultimate DIY Lean-To Shed: Step-by-Step Plans for Outdoor Bliss
Tired of battling the elements while tending your garden or storing your outdoor equipment? A lean-to shed offers the perfect blend of practicality and aesthetic appeal, providing sheltered space without overwhelming your backyard. This comprehensive guide empowers you to build your own, transforming your outdoor area into a haven of organization and convenience. Forget overpriced, pre-fabricated sheds; embrace the rewarding experience of crafting a personalized structure tailored to your specific needs. Let's dive into this fulfilling DIY project!
Planning Your Perfect Lean-To Shed
Before you grab your tools, careful planning is crucial. Determine the shed's intended purpose. Will it house gardening supplies, bicycles, or serve as a workshop? This dictates the size and features you'll need. Consider your available space, ensuring the shed's dimensions complement your existing landscape without feeling cramped or imposing. Sketch a detailed plan, noting precise measurements for the walls, roof, and foundation. Factor in the location's sun exposure to optimize natural light and ventilation. Don't forget to check local building codes and obtain any necessary permits before breaking ground. This proactive approach ensures a smooth, legally compliant project.
Essential Materials & Tools
Gathering the right materials and tools is paramount for a successful build. You'll need pressure-treated lumber for durability, roofing materials (shingles, metal, or polycarbonate panels), concrete for the foundation (or alternative like gravel), screws, nails, and appropriate fasteners. Invest in quality tools such as a saw (circular saw or hand saw), drill, level, measuring tape, and safety glasses. A post hole digger will simplify foundation work. Prepare a comprehensive shopping list to avoid mid-project delays. Remember to purchase extra materials to account for potential errors or unforeseen needs.
Foundation & Framing: Building the Base
Begin by preparing the foundation. For a stable base, dig holes and pour concrete footings to support your vertical supports. Alternatively, use a gravel base for a less permanent solution. Next, erect the frame. Attach the vertical posts securely to the foundation, ensuring they are perfectly plumb. Use a level frequently to guarantee accuracy. Then, attach horizontal beams to create the wall frame. Precise measurements and strong bracing are key to a robust and long-lasting structure. Take your time; accuracy at this stage prevents problems later on.
Roof Construction: Protecting Your Investment
Roof construction requires careful attention to detail. Attach rafters to the top of the frame, ensuring they slope appropriately to facilitate water runoff. Use appropriate fasteners and reinforce connections for added strength. Install sheathing over the rafters to create a solid base for your roofing material. Finally, lay your chosen roofing material, following the manufacturer's instructions carefully. Remember, a well-constructed roof safeguards your shed's contents and prolongs its lifespan. Carefully inspect your work at each stage.
Finishing Touches: Adding the Personal Flair
Once the main structure is complete, add the finishing touches to personalize your lean-to shed. Consider adding a door for easy access. You can install simple shelving to maximize storage, or add a workbench if it's a workshop. Paint the exterior to blend with your surroundings or add a pop of color. Consider adding weather stripping around the door and windows for enhanced insulation and protection from the elements. These finishing touches transform your functional shed into a truly personalized space.
Safety First!
Throughout the entire process, prioritize safety. Always wear appropriate safety gear, including safety glasses, work gloves, and sturdy footwear. Use caution when operating power tools and follow the manufacturer's instructions carefully. Take breaks when needed to prevent fatigue and maintain focus. Working safely ensures a smooth project and prevents potential injuries.
Building your own lean-to shed is a rewarding experience that combines skill, creativity, and hard work. With careful planning and attention to detail, you'll create a valuable addition to your outdoor space, a testament to your DIY prowess, and a source of immense satisfaction for years to come.
Friday, November 15, 2024
12x20 Shed with Loft Blueprints: Detailed Designs for DIYers

12x20 Shed with Loft Blueprints: Detailed Designs for DIYers
This document provides comprehensive blueprints and design specifications for constructing a 12x20 foot shed with a loft. Intended for experienced DIYers, these plans detail the entire construction process, from foundation to finishing touches. Careful review and understanding of these plans are crucial before commencing construction. Improper execution may compromise structural integrity and safety.
I. Foundation and Site Preparation
A robust foundation is paramount for a long-lasting structure. The chosen foundation type will depend on several factors, including soil conditions and local building codes. Consult with a local building inspector to determine the appropriate foundation for your site.
A. Site Selection and Preparation
Select a level area with adequate drainage. Clear the area of vegetation, debris, and any obstacles. Mark out the 12x20 foot area precisely using stakes and string. Ensure accurate measurements are taken to avoid future complications.
B. Foundation Options
Several foundation options exist, each with its own advantages and disadvantages:
- Concrete Slab: Provides a strong, level base but requires significant excavation and concrete pouring. This is generally the most robust option.
- Gravel Base with Pressure-Treated Skids: A more cost-effective option, suitable for well-drained soil. Requires less excavation but may require more maintenance over time.
- Pier and Beam Foundation: Ideal for uneven terrain. Requires precise placement of piers and robust beam construction.
Note: Detailed specifications for each foundation type, including material quantities and construction techniques, are provided in the accompanying detailed blueprints.
II. Framing and Structure
The framing forms the skeletal structure of the shed and must be meticulously constructed to ensure stability and longevity. Pressure-treated lumber is recommended for all ground-contact components to resist rot and insect damage.
A. Floor Framing
The floor framing consists of pressure-treated sill plates, floor joists, and subflooring. Joists should be spaced appropriately (typically 16 inches on center) and securely fastened to the sill plates and to each other using appropriate fasteners. Engineered wood I-joists can be considered for longer spans to minimize deflection.
B. Wall Framing
Wall framing utilizes standard framing techniques. Construct wall panels on the ground for ease of assembly. Use appropriate sized lumber for studs (typically 2x4s or 2x6s) and ensure proper spacing and bracing. Install windows and doors during this stage.
C. Roof Framing
The roof framing can be either a gable or a shed roof. Detailed plans for both are provided. Rafters must be properly calculated to ensure adequate support for the roof load. Consider using ridge boards and purlins for added strength and stability. Properly slope the roof to facilitate water runoff.
D. Loft Framing
The loft framing necessitates additional support beams and joists. These must be securely connected to the main structure. Proper calculations for load-bearing capacity are crucial for safety. Consider using engineered lumber for the loft floor joists to minimize deflection and maximize load-bearing capacity.
III. Exterior Cladding and Roofing
The exterior cladding and roofing protect the shed from the elements. Choose materials that are durable, weather-resistant, and aesthetically pleasing. Adherence to local building codes regarding fire safety and wind resistance is essential.
A. Siding Options
Several siding options are available, each with its own advantages and disadvantages:
- Vinyl Siding: Low maintenance and relatively inexpensive, but can be damaged easily.
- Wood Siding: Classic look, but requires regular maintenance and painting.
- Metal Siding: Durable and weather-resistant, but can be more expensive.
B. Roofing Materials
Roofing materials should be chosen based on local climate conditions and budget:
- Asphalt Shingles: Cost-effective and widely available.
- Metal Roofing: Durable and long-lasting, but can be more expensive.
C. Installation
Detailed instructions for installing siding and roofing materials are provided in the accompanying blueprints. Proper flashing and sealing are crucial to prevent water leakage. Ensure all nails and screws are appropriately sized and driven to prevent damage to the materials.
IV. Interior Finishing and Loft Access
Interior finishing adds functionality and aesthetics to the shed. The loft access should be carefully planned and constructed to ensure safety and ease of use.
A. Interior Walls and Ceiling
The interior walls and ceiling can be finished with drywall, plywood, or other suitable materials. Consider insulation for added comfort and energy efficiency.
B. Loft Access
The loft access can be a fixed staircase or a retractable ladder. Choose the option that best suits your needs and the available space. Ensure that the access point meets safety regulations.
C. Electrical and Plumbing
If electrical or plumbing is required, ensure that all work is carried out by qualified professionals and meets all applicable codes. Proper grounding and safety measures must be implemented.
V. Safety Precautions
Safety is paramount throughout the construction process. Always wear appropriate safety gear, including safety glasses, gloves, and hearing protection. Follow all manufacturer's instructions for tools and materials. Obtain necessary permits before commencing construction and adhere to all local building codes.
This document provides a general overview. The accompanying detailed blueprints contain precise measurements, material lists, and step-by-step instructions. It is crucial to carefully study and understand these blueprints before initiating the construction of your 12x20 shed with loft. Any deviation from these plans could compromise structural integrity and safety.
Monday, November 11, 2024
How to Design a Pole Barn with Ample Storage for Seasonal Items
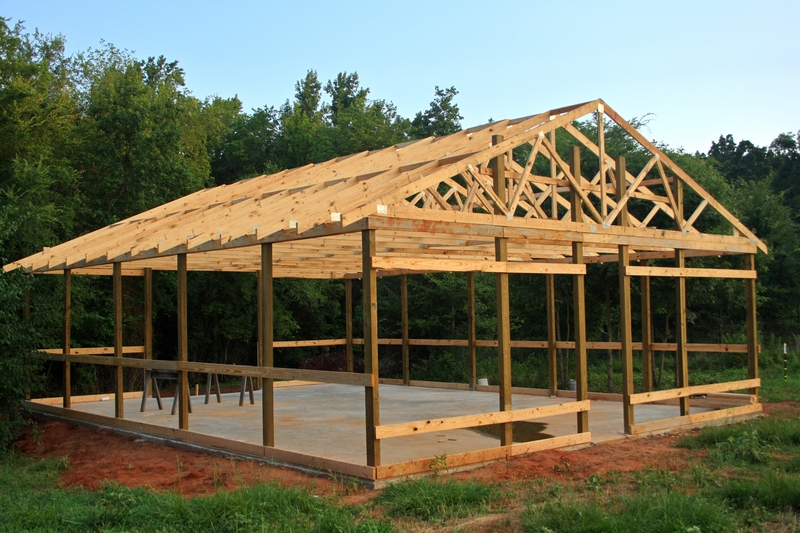
Okay, let's talk pole barns. You know, those sturdy, practical structures that have become synonymous with storage, workshops, and even living space. But we're going to focus on the storage part, specifically for all that seasonal stuff that takes over your garage or basement. Think kayaks, lawnmowers, holiday decorations, winter gear â" you name it, it's going to have a place in your new pole barn paradise.
Step 1: Dream Big, But Be Realistic
Before you start sketching out your perfect pole barn on a napkin (we've all been there!), let's get real. Think about the space you actually need. How much stuff are we talking about? Are you planning on storing vehicles, too?
Here's a little exercise to get you started:
List everything: Write down every single item you want to store in the barn.
Categorize: Group items into categories (e.g., lawn and garden, sports equipment, holiday décor, etc.)
Measure: Go through your list and actually measure the dimensions of each item. This is crucial for planning your layout.
Step 2: Planning the Layout â" It's All About Flow
Now that you know what you're working with, you can start to plan the layout. Imagine yourself moving through the barn â" where will you enter? Where will you store the most-used items? Where can you park a vehicle, if needed?
Think vertical: Utilize vertical space with shelves, racks, and even overhead storage systems. You'd be surprised how much you can store by going up!
Leave room to breathe: Don't cram everything in, leaving no room to move around. Allow for aisles and walkways for easy access.
Consider future needs: Will you need to add more storage in the future? Plan for expansion. Maybe have a small section designated for future additions.
Step 3: Choosing Your Pole Barn Materials â" The Basics
Pole barns are known for their durability and affordability. But there are a few things to consider when choosing materials:
Posts: Typically made of treated lumber, steel, or concrete. Treated lumber is cost-effective, while steel and concrete offer superior durability.
Roofing: Metal roofing is a popular choice due to its longevity and affordability. It also provides good insulation.
Siding: Vinyl siding is a good option for low maintenance, while metal siding is more durable.
Windows and Doors: Consider adding plenty of windows for natural light and ventilation. Choose a door size that allows you to easily move large items in and out.
Step 4: Beyond the Basics â" Adding Your Personal Touch
Your pole barn is going to be more than just storage; it's an extension of your home. Think about how you want to use the space and add some personal touches:
Work area: Designate a corner for a workbench, tools, and project supplies.
Lighting: Proper lighting is essential for working and safety. Consider LED lighting for energy efficiency.
Heating and cooling: If you plan to spend time in the barn, consider adding heating and cooling systems.
Flooring: Concrete floors are durable but can be cold. Consider adding a layer of epoxy or adding mats for comfort.
Step 5: The Finishing Touches â" Making it Your Own
Now for the fun part â" adding your personal flair to the space.
Wall colors: Choose a neutral color that reflects light, or add pops of color to define different areas.
Organization systems: Invest in storage solutions that fit your needs, such as shelves, bins, and hooks.
Decor: Add a few personal touches, like a vintage sign, a cozy armchair, or even a mini fridge for those long working days.
Here are some ideas for maximizing storage space:
Ceiling Storage: Install overhead storage systems for those items you don't use often, such as holiday decorations or seasonal clothing.
Vertical Storage Racks: Use wall-mounted racks for tools, sporting equipment, and even bikes.
Sliding Doors: Optimize space by installing sliding doors instead of traditional swing doors, especially if you have limited space.
Utilize the Walls: Use pegboards, shelves, and hooks to keep tools and accessories organized and easily accessible.
Go Up! Think about adding a loft for additional storage or even a workspace.
Don't forget the fun part! Remember, this is your space to enjoy. Add some personal touches, make it comfortable, and make it reflect your personality.
Building a pole barn is a great way to gain valuable storage space and add value to your property. By following these tips, you can create a functional and beautiful space that you'll love for years to come.
DIY Pole Barn Plans for Your Farm or Homestead
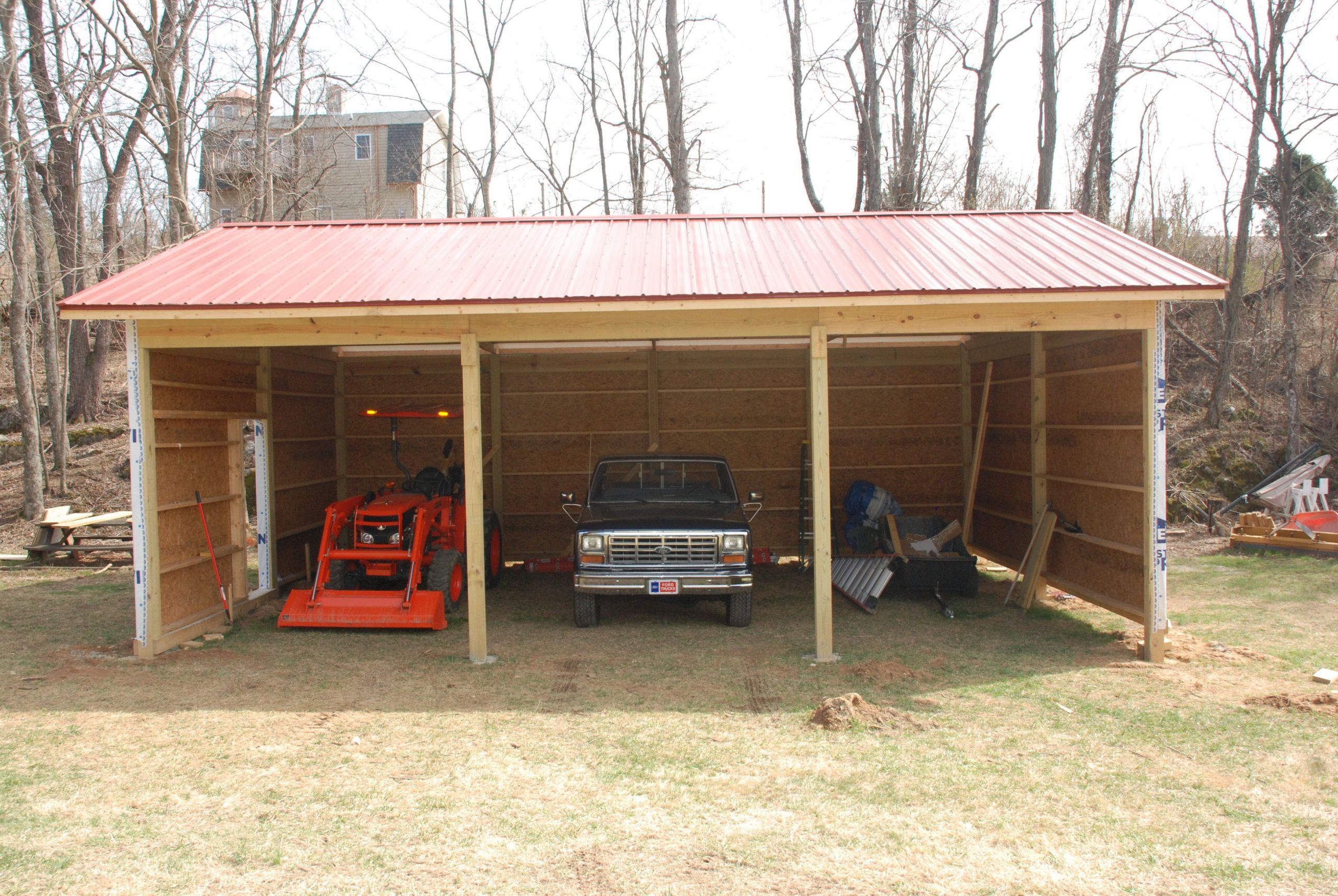
Hey there, fellow homesteaders! Ever dreamed of a big, beautiful pole barn to house all your tools, equipment, and maybe even a few furry friends? Building your own pole barn is a great way to get the space you need without breaking the bank. It's a project that might seem daunting at first, but trust me, it's way more doable than you think!
Why Choose a Pole Barn?
First things first, why are pole barns so darn popular with homesteaders? Let's break it down:
Cost-Effective: Compared to traditional stick-built structures, pole barns are budget-friendly. You're using less material, and the simplicity of the design means less labor.
Easy to Build: The basic construction is straightforward, making it a great project for DIYers with some experience.
Versatile: Pole barns are incredibly adaptable! Use them for storage, workshops, animal shelters, even living space with some creative planning.
Strong and Durable: Pole barns are built to last! The sturdy posts and open structure withstand heavy loads and the elements.
The Planning Stage: Getting Your Ducks in a Row
Before you grab your tools, it's essential to plan your project like a seasoned farmer! Here's what to think about:
1. Design and Size: What will you use the barn for? That'll determine your size and shape. Do you need a wide open space for equipment or a few stalls for horses?
2. Location, Location, Location: Consider the location of your barn on your property. Think about access, drainage, and proximity to existing utilities. A good rule of thumb is to make sure it's accessible by a truck or tractor.
3. Permits and Codes: Check with your local building department. They'll tell you about any specific requirements for pole barns in your area.
4. Budget and Materials: Do your research! Different types of wood and metal will affect your cost. Plan to factor in everything from lumber to concrete to roofing materials.
5. Tools and Equipment: You'll need a basic set of tools for construction, including a tape measure, level, circular saw, hammer, drill, and concrete mixer. You may also want to consider renting heavy equipment, like a post hole digger or a skid steer.
Getting Started: The Foundation of Your Barn
Now comes the fun part: building the foundation! Here's the basic process:
1. Preparing the Site: Clear the area, mark the location of the posts, and level the ground.
2. Digging the Holes: This is where your post hole digger or skid steer comes in handy! Dig holes for your support posts, making sure they're deep enough to be below the frost line.
3. Concrete Forms: If you're using concrete piers, create forms to hold the concrete in place.
4. Setting the Posts: Place the posts in the holes, making sure they're plumb and level. Secure them with temporary bracing.
5. Pouring Concrete: Once the forms are set, pour concrete into the holes to secure your posts. Let the concrete cure properly.
Framing the Barn: Raising the Roof
With your foundation secure, it's time to build the framework!
1. Setting the Ridge Beam: Place the ridge beam on top of the posts, securing it with metal brackets.
2. Installing Rafters: Cut and install the rafters, making sure they're properly spaced.
3. Sheathing the Roof: Attach plywood or OSB sheathing to the rafters to create a solid roof deck.
4. Installing Walls: Frame the walls using stud walls or prefabricated wall panels. Remember to allow for windows and doors!
Finishing Touches: Bringing Your Barn to Life
Once the basic framing is done, it's time to make your barn your own!
1. Roofing: Choose your roofing material based on your budget and style. Metal roofing is durable and popular for pole barns.
2. Siding: Siding options range from traditional wood to modern metal panels.
3. Windows and Doors: Add windows and doors for light, ventilation, and access.
4. Insulation and Finishing: If you plan on using the barn for living space or a workshop, add insulation to keep it comfortable. Finish the interior with drywall or other wall coverings.
A Little Bit of Advice:
Safety First: Always wear safety glasses and follow proper construction practices.
Don't Be Afraid to Ask for Help: There's no shame in enlisting help from friends, family, or professional contractors.
Enjoy the Process: Building your own pole barn is a rewarding experience! Take your time, celebrate your progress, and enjoy the fruits of your labor.
Building your own pole barn can be a lot of work, but it's also a rewarding experience! It's a chance to create a custom space that perfectly suits your needs, and it's a project you can be proud of for years to come.
Remember, this is just a basic overview. There are many different designs and techniques for building pole barns. Be sure to do your research and consult with a professional if needed. Happy building!
How to Design a Pole Barn for Your Specific Storage Needs

A pole barn, also known as a post-frame building, offers a versatile and cost-effective solution for a wide range of storage needs. Whether you require space for vehicles, equipment, livestock, or simply extra room for household items, a well-designed pole barn can serve as a practical and durable asset. This guide will provide a comprehensive overview of the design process, ensuring your pole barn meets your specific requirements.
1. Defining Your Needs and Goals:
Begin by meticulously outlining your storage needs. Consider the following:
Purpose: What will the pole barn primarily store? Vehicles, equipment, hay, livestock, or a combination?
Size: Determine the minimum square footage required to accommodate your belongings. Factor in aisle space for easy maneuverability.
Height: Ensure sufficient vertical clearance for vehicles, equipment, or potential future storage needs.
Doorways and Windows: Plan for appropriately sized doors for vehicle access, as well as potential windows for natural light and ventilation.
Flooring: Will the floor need to be concrete for heavy equipment or gravel for easier drainage?
Utilities: Do you require electricity, water, or other utilities?
Budget: Establish a realistic budget to guide design decisions.
2. Site Selection and Considerations:
Selecting the right site is crucial for optimal pole barn placement. Consider factors such as:
Accessibility: Ensure easy access for vehicles and deliveries.
Drainage: Choose a site with good drainage to prevent water accumulation around the building.
Zoning regulations: Confirm the site complies with local zoning ordinances related to building size, setbacks, and permitted uses.
Soil conditions: Investigate the soil type to determine if it's suitable for supporting the pole barn foundation.
Sun exposure: Evaluate the site's sun exposure for potential natural lighting and solar energy options.
Wind exposure: Consider the site's wind exposure, as it can affect the building's structural stability.
3. Design and Planning:
Once your needs are defined and the site selected, begin designing your pole barn:
Structural Integrity: Consult with a qualified engineer to ensure the building meets local building codes and withstands anticipated loads. Consider factors like snow load, wind load, and potential future additions.
Foundation Design: Select a foundation type suitable for the soil conditions and anticipated loads. Common options include concrete piers, helical piles, or a combination.
Framing and Construction: Pole barns typically utilize vertical posts, girders, and trusses. Choose materials like treated lumber or steel for longevity and durability.
Roofing and Siding: Select roofing and siding materials that align with your budget and aesthetic preferences. Consider options like metal roofing, vinyl siding, or composite materials.
Insulation: Evaluate insulation needs based on your climate and intended use. Insulation can improve energy efficiency and create a more comfortable environment.
Ventilation: Plan for adequate ventilation to ensure proper air circulation, prevent moisture build-up, and create a healthier storage environment.
4. Essential Considerations for Specific Storage Needs:
Vehicle Storage:
Driveway and Parking: Plan for a wide and accessible driveway to accommodate vehicle movement.
Door Height and Width: Ensure doors are large enough to accommodate the tallest vehicles.
Floor Strength: Choose a strong concrete floor capable of supporting the weight of vehicles.
Equipment Storage:
Overhead Clearance: Provide sufficient height for tall equipment, including hoists or forklifts.
Shelving and Storage Systems: Consider incorporating shelves, racks, or other storage systems to optimize space.
Electrical Outlets and Lighting: Ensure adequate electrical outlets and lighting for operating equipment.
Livestock Storage:
Ventilation and Climate Control: Ensure proper ventilation and temperature control for animal comfort.
Water and Feed Storage: Plan for convenient storage of water and feed for livestock.
Manure Management: Consider manure handling systems for efficient waste removal.
Household Storage:
Organization: Designate specific areas for different categories of belongings.
Shelving and Storage Solutions: Utilize shelves, cabinets, and drawers for organized storage.
Lighting and Security: Install adequate lighting and security systems for peace of mind.
5. Choosing a Contractor:
Select a reputable contractor experienced in pole barn construction. Request bids from multiple contractors, comparing pricing, experience, and references. Ensure the contractor is licensed, bonded, and insured.
6. Permitting and Inspections:
Obtain necessary permits and inspections from local authorities before beginning construction.
7. Final Touches and Maintenance:
Once construction is complete, consider adding finishing touches like landscaping, paint, or decorative accents. Implement a regular maintenance schedule to ensure the longevity of your pole barn.
Conclusion:
Designing a pole barn for your specific storage needs requires meticulous planning and attention to detail. By carefully considering factors like site selection, structural integrity, and specific storage requirements, you can create a functional, durable, and aesthetically pleasing building that will serve you for years to come. Remember to consult with qualified professionals throughout the process to ensure your pole barn meets local building codes and is tailored to your unique storage needs.
How to Build a Pole Barn with Heavy-Duty Floor Construction
Pole barns, known for their versatility and cost-effectiveness, provide a robust solution for a variety of uses, from agricultural storage to workshops and garages. However, the success of any pole barn hinges on a strong foundation, especially when dealing with heavy equipment or demanding usage. This article delves into the meticulous process of constructing a pole barn with heavy-duty floor construction, emphasizing durability and longevity.
1. Site Preparation and Planning
a. Site Selection and Soil Testing:
The first step involves selecting a suitable site with appropriate drainage and minimal soil movement. Conducting a soil test is crucial to understand the soil composition and bearing capacity. This information will inform the choice of foundation design, ensuring adequate support for the structure and the heavy-duty floor.
b. Site Clearing and Grading:
Once the site is chosen, it needs to be cleared of any vegetation, debris, and existing structures. Grading the site involves leveling the ground to achieve a uniform slope, ensuring proper drainage and preventing water accumulation.
c. Determining the Pole Barn's Size and Layout:
Define the desired dimensions of the pole barn, taking into account the intended use, equipment storage, and accessibility requirements. Create a detailed plan outlining the placement of doors, windows, and internal features.
2. Foundation Construction: Laying the Groundwork for Durability
a. Concrete Piers and Footing:
The foundation of a heavy-duty pole barn floor typically involves constructing concrete piers, which act as support points for the floor system. These piers are embedded in the ground and connected by a reinforced concrete footing.
b. Concrete Slab Design and Reinforcement:
The floor slab design should account for the anticipated loads and traffic patterns. Reinforcement bars are incorporated within the concrete slab to enhance its tensile strength and prevent cracking.
c. Grading and Compaction:
Prior to pouring the concrete, the prepared area must be graded and compacted thoroughly. This ensures a stable and level surface for the concrete slab, minimizing settling and unevenness.
3. Floor Construction: Building a Foundation for Strength
a. Insulation and Vapor Barrier:
Insulating the floor beneath the concrete slab helps to reduce heat loss and improve energy efficiency. A vapor barrier is installed to prevent moisture from penetrating the insulation and potentially causing damage to the floor.
b. Gravel Base:
A layer of gravel is laid over the compacted soil, providing a drainage layer and enhancing the load-bearing capacity of the floor. This base serves as a buffer between the concrete slab and the underlying soil.
c. Concrete Slab Placement and Finishing:
Once the gravel base is in place, the concrete slab is poured and finished. It is vital to ensure proper consolidation and vibration of the concrete to achieve optimal density and strength.
4. Pole Frame Construction: Creating a Stable Framework
a. Pole Placement and Erection:
The pole frame is erected directly onto the concrete piers, providing structural support for the roof and walls. The poles, typically made of treated lumber or steel, are spaced according to the design specifications.
b. Wall Construction and Bracing:
The walls are constructed using various materials such as wood framing, metal siding, or concrete blocks. Bracing is essential to ensure stability and prevent the walls from bowing or collapsing under load.
c. Roof Construction and Framing:
The roof frame, often constructed using trusses, is attached to the pole frame and supports the roofing material. The choice of roofing material depends on the intended use of the pole barn and local climate conditions.
5. Heavy-Duty Floor Considerations:
a. Floor Finish:
The choice of floor finish depends on the intended use of the pole barn. Options include concrete, epoxy coatings, rubberized flooring, or specialized flooring for heavy equipment.
b. Load Capacity and Traffic Patterns:
When planning the heavy-duty floor construction, carefully consider the anticipated loads and traffic patterns. The floor design should accommodate heavy equipment, forklift traffic, and other potential stresses.
c. Drainage and Ventilation:
Proper drainage and ventilation are essential to prevent moisture buildup and ensure a healthy environment within the pole barn. Incorporating drains and ventilation systems helps to control moisture and maintain air quality.
6. Finishing Touches: Enhancing Functionality and Aesthetics
a. Doors and Windows:
Installing durable doors and windows ensures accessibility and provides natural lighting. The size and placement of doors and windows should align with the intended use of the pole barn.
b. Electrical Wiring and Plumbing:
Electrical wiring and plumbing systems should be installed according to local codes and regulations. The placement and capacity of electrical outlets and plumbing fixtures should be considered based on the pole barn's intended purpose.
c. Interior and Exterior Finishes:
Finishing touches such as paint, siding, and insulation enhance the aesthetics and functionality of the pole barn. The choice of finishes should complement the overall design and intended use of the structure.
Conclusion
Constructing a pole barn with heavy-duty floor construction demands meticulous planning, careful execution, and adherence to building codes. The foundation, floor, and frame should be designed to withstand the anticipated loads and ensure long-term durability. By carefully following these steps, you can create a robust and reliable pole barn that meets your specific needs and stands the test of time. Remember, consulting with qualified professionals, such as architects, engineers, and contractors, is crucial for ensuring a successful and safe construction project.
Sunday, November 10, 2024
Building a long-lasting 12x20 storage shed

Hey there, fellow DIYer! So, you're thinking about building a shed, eh? Good choice! A shed is a great way to tidy up your yard, organize your life, and maybe even add some value to your property. But let's be real, building anything from scratch can be a bit daunting. That's why I'm here to guide you through building a sturdy, long-lasting 12x20 storage shed that'll stand the test of time... and maybe even outlast you!
Now, before we get into the nitty-gritty, let's talk about what makes a good shed, especially one that's gonna stand strong against Mother Nature. We're going for durability here, and that means choosing the right materials, building a solid foundation, and making sure everything is properly sealed.
### First Things First: The Foundation
Think of the foundation as the backbone of your shed. It's the crucial first step that'll determine how stable and long-lasting your shed will be. Now, there are different ways to build a foundation, but for a 12x20 shed, you've got a few solid options:
Concrete Slab: This is the most durable and long-lasting foundation. It's basically like pouring a big, flat slab of concrete. This option is great if you have a relatively level area and you're willing to put in the time and effort. It requires some digging, but the payoff is a foundation that can handle even the heaviest loads.
Concrete Pier Foundation: This is a bit more complex than a slab, but it's still a good option for a shed. It involves placing concrete piers in strategic spots and then connecting them with wooden beams. This method is good for uneven ground and can handle heavier loads.
Wooden Skids: This is the simplest and cheapest option. It involves placing pressure-treated wooden skids on the ground to support the shed's frame. It's easy to assemble and is best for light-duty sheds on level ground. However, it's less durable than concrete options and may require re-leveling over time.
Pro Tip: If you're going for a concrete foundation, make sure you get the measurements right! You don't want to have a foundation that's too small or too large for your shed.
### Building the Frame: The Bones of Your Shed
Now that your foundation is set, it's time to build the framework. For a 12x20 shed, you'll need to use 2x6 or 2x8 lumber for the floor joists and wall studs.
Here's the breakdown:
Floor Joists: Lay them down on top of the foundation and secure them using joist hangers.
Wall Studs: These are the vertical supports for your walls. Spacing them 16 inches apart will give your shed the strength it needs.
Roof Trusses: You can purchase pre-made trusses or build them yourself. Make sure to use a building plan for proper sizing and spacing.
Pro Tip: Use pressure-treated lumber for the foundation and floor joists, as it's resistant to moisture and decay. And remember to always wear safety glasses and gloves when working with lumber!
### Putting on the Skin: Siding and Roofing
Now for the fun part: adding the exterior! This is where you get to choose the look and feel of your shed. For siding, you have plenty of options:
Vinyl Siding: It's budget-friendly, easy to install, and requires minimal maintenance.
Wood Siding: It's a classic choice that adds charm and character. There are different types of wood to choose from, each with its own look and durability.
Metal Siding: It's durable, weather-resistant, and comes in various colors and textures.
For the roof, you've got a few choices, too:
Shingles: They're popular for their durability and affordability.
Metal Roofing: It's long-lasting, low-maintenance, and can withstand harsh weather conditions.
Rubber Roofing: It's lightweight and water-resistant, making it a good choice for shed roofs.
Pro Tip: Make sure to choose a roof that's properly ventilated to prevent moisture buildup.
### Don't Forget the Details!
Doors and Windows: Choose the size and style that suits your needs.
Insulation: Add insulation to keep your shed warm in the winter and cool in the summer.
Painting: Protect your shed and give it a fresh look with a good coat of paint.
### Taking Care of Your Shed: Long-Term Maintenance
Alright, you've built a beautiful and durable shed. Now, to keep it that way, you've got to maintain it! Here's what you need to do:
Regular Inspection: Check for any cracks, loose boards, or signs of water damage.
Cleaning: Sweep the floor and remove any debris.
Painting: Repaint the shed every few years to protect it from the elements.
Roof Maintenance: Check the shingles or metal panels for any damage and replace them as needed.
### Wrapping Up
Building a shed might seem like a big undertaking, but with proper planning and the right steps, it can be a rewarding project. It's not just about building a storage space; it's about creating a space that adds functionality and character to your property.
Remember, it's about taking your time, being patient, and taking pride in your work. So, get out there, gather your tools, and start building that shed you've always dreamed of! You've got this!
Top-rated 10x12 storage shed plans for any budget
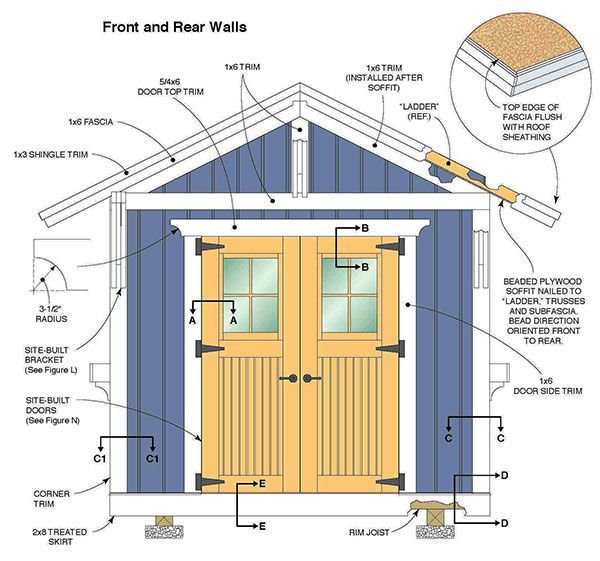
Hey there, fellow shed-dreamers! Are you staring at that overflowing garage or cluttered backyard and wishing for a little extra space? Well, you're not alone. A 10x12 storage shed is the perfect solution for many homeowners, offering a generous 120 square feet of space without taking up a ton of your property. But with so many options out there, where do you even start?
Don't worry, I've got you covered! I'm diving deep into the world of 10x12 storage shed plans, breaking down everything from budget-friendly DIY to pre-fab kits to professional builds. No matter your skill level or budget, you'll find the perfect plan to turn your storage woes into a sleek and functional shed!
The DIY Route: For the Crafty and Cost-Conscious
Let's face it, building a shed yourself is a rewarding challenge (and a great way to save some serious cash!). You'll be amazed at the range of DIY 10x12 storage shed plans available online and in home improvement stores. They're usually pretty easy to follow and provide detailed instructions with diagrams and cutting lists.
Here's what you'll love about DIY:
Budget-friendly: This is the most cost-effective option, allowing you to control every penny spent. You can source materials from various places, including local lumberyards, big box stores, and even salvage yards!
Personalized design: Want a gable roof or a hip roof? A traditional style or something more modern? With DIY, you can customize your shed to fit your exact preferences!
Sense of accomplishment: There's nothing quite like seeing your own creation come to life! Building a shed from scratch is a fantastic learning experience and a great way to boost your confidence.
Ready to jump in? Here's a breakdown of what you'll need:
Plan: Choose a plan that fits your skills and the materials available in your area. Make sure to factor in the type of foundation you'll need (concrete, pier blocks, or wooden skids).
Materials: You'll need lumber, roofing materials, siding, windows, doors, and hardware. Double-check the plan's materials list and create a detailed shopping list.
Tools: Depending on the plan, you'll need basic carpentry tools like a circular saw, drill, hammer, tape measure, and level. Don't forget safety gear like gloves, safety glasses, and hearing protection!
DIY Tip: Start small! If you're new to building, consider tackling a smaller project first, like a birdhouse or a playhouse. This will give you the confidence and experience you need to tackle a larger shed project.
Pre-Fab Kits: The Middle Ground for Convenience and Cost
If the idea of DIY sounds a bit daunting, but you're still looking to save money, pre-fab kits are a fantastic option. These kits contain all the pre-cut lumber, hardware, and instructions you need to assemble your 10x12 storage shed.
What makes pre-fab kits so appealing?
Simplified construction: They take away the stress of measuring and cutting lumber, making the process much easier.
Clear instructions: Pre-fab kits come with detailed instructions, making the building process more manageable, even for beginners.
Wide range of styles: You can find a variety of styles and materials, from basic wooden sheds to metal sheds with more modern looks.
But there are a few things to keep in mind before taking the plunge:
Limited customization: While some kits allow for some customization, you're generally limited to the pre-determined design and features.
Foundation requirements: You'll still need to choose and build the foundation yourself, so don't forget to factor that into your planning.
Delivery and assembly: You'll need to factor in the cost of delivery and the time needed to assemble the shed, especially if you don't have any carpentry experience.
Pro Tip: Shop around! Compare prices and features between different manufacturers to find the best deal for your needs.
Professional Builds: For a Stress-Free Experience
If you value convenience above all else, or you just don't have the time or skills for DIY, hiring a professional contractor is the way to go. A contractor will handle all the planning, permits, materials sourcing, and construction, leaving you to relax and enjoy the process!
Here's why hiring a professional might be the right choice for you:
Stress-free construction: Let the professionals handle the heavy lifting, the complicated cuts, and the potential headaches.
Professional expertise: Contractors have the experience and knowledge to build a sturdy and long-lasting shed.
Warranty and insurance: Many contractors offer warranties on their work, giving you peace of mind and protection against any potential issues.
But remember, professional builds come with a higher price tag:
Labor costs: You'll be paying for the contractor's expertise and time.
Materials markup: Contractors may charge a markup on materials, so it's good to do your research and get multiple quotes.
Permit fees: These are generally handled by the contractor, but they will be reflected in the final cost.
To get the most out of your professional build:
Get multiple quotes: Don't settle for the first contractor you find. Get quotes from at least three different companies and compare their services and prices.
Ask about permits: Make sure the contractor handles all necessary permits and inspections.
Discuss your needs and budget: Be clear about what you want from your shed and how much you're willing to spend. Communicate openly with the contractor to ensure your expectations are aligned.
No matter which route you choose, remember to:
Consider your needs: How will you be using your shed? Will you need electricity? Will you be storing heavy items?
Check local codes and regulations: Before you start building, make sure your shed design complies with local building codes and zoning laws.
Plan for the future: Think about how your shed will be used in the long run. Will you need to expand it later? Will you need to add any special features?
Now you're ready to embark on your shed-building journey! Whether you're a seasoned DIY enthusiast or someone who prefers to delegate, there's a perfect 10x12 storage shed plan out there waiting for you. With a little planning, effort, and a touch of imagination, you'll be enjoying your new storage space in no time! Happy building!
Tips for building a 12x20 storage shed on a budget

Okay, so you're thinking about building a storage shed. Maybe you've got a bunch of stuff taking up space in the garage, or you're finally getting around to organizing that overflowing attic. Whatever the reason, a shed can be a total lifesaver. And, let's be honest, who doesn't love a little DIY project?
But here's the catch: building a shed isn't exactly cheap. Those pre-made sheds can be pretty pricey, and hiring a contractor to build one for you? Forget about it! But don't worry, you can totally build a 12x20 shed on a budget, you just gotta get a little creative.
First things first: Planning and Design
Before you even think about grabbing a hammer, you gotta have a solid plan. I'm talking about a plan that's so detailed, you could build the shed in your sleep (though I wouldn't recommend it).
Here's what to consider:
Location, location, location! Pick a spot for your shed that's flat, dry, and easily accessible. You'll also want to make sure it's far enough away from your house that you don't have to worry about fire codes or blocking windows.
Building codes and permits: Don't skip this step! Check with your local building department about the requirements for sheds in your area. Some places are pretty relaxed, while others have specific rules about size, materials, and even the color of your shed.
Decide on your design: Do you want a basic shed with a single door, or something more elaborate with windows and a loft? What kind of roof do you want? Think about how you'll be using the shed and what features are important to you.
Choose your materials: This is where you can really start to save money. Consider using reclaimed lumber or wood from a local lumberyard. There are also affordable shed kits available online that can save you a lot of time and hassle.
Now let's talk about the building process:
Foundation: A simple concrete slab is the most common and affordable foundation for a shed. You can pour it yourself (check out some tutorials on YouTube, it's not as hard as you think!), or hire a contractor to do it for you.
Framing: This is the backbone of your shed, and it's important to get it right. Use pressure-treated lumber for the bottom plates and joists to prevent rot. You can get framing lumber at your local hardware store, and there are also kits available online that can help you get started.
Sheathing: This is the layer that goes on top of the framing to create a solid surface for your siding. Plywood is the most common material used for sheathing, and you can save money by using standard grade plywood for the interior walls.
Roofing: Asphalt shingles are the most affordable option for roofing, and they're relatively easy to install. You can also get pre-made roofing panels that make installation even faster.
Siding: Vinyl siding is a popular choice for sheds because it's durable, low-maintenance, and comes in a variety of colors. Wood siding is also an option, but it requires more upkeep.
Doors and windows: Shop around for doors and windows that fit your budget. You can often find good deals on used doors and windows at local salvage yards or online.
Finishing touches: Once the basic structure is complete, you can add finishing touches like paint, trim, and hardware. Don't be afraid to get creative and make your shed your own!
Cost-saving Tips:
DIY is your friend! The more you do yourself, the less you'll have to pay for labor. Start with basic skills like measuring, cutting, and nailing, and gradually work your way up to more complex tasks.
Shop around for materials: Don't settle for the first price you see. Get quotes from multiple lumberyards and hardware stores to find the best deals.
Look for reclaimed materials: Reclaimed lumber is often available at affordable prices, and it's a great way to give your shed a unique look. Check out salvage yards, demolition sites, and online marketplaces.
Consider a shed kit: Shed kits can save you a lot of time and money, especially if you're not experienced with building. They usually include all the materials you need, along with instructions and blueprints.
Don't be afraid to ask for help: If you're stuck on a particular step, don't be afraid to ask a friend or family member for help. You can also find plenty of DIY resources online and in libraries.
And remember, building a shed is about more than just saving money; it's about creating something beautiful and functional that you can enjoy for years to come. So relax, have fun, and don't be afraid to experiment!
Here's a breakdown of some potential costs to consider:
Materials: $1,500 - $3,000 (depending on the size, design, and materials used)
Foundation: $500 - $1,000 (depending on the size and type of foundation)
Labor: $0 - $1,000 (depending on how much DIY you do)
Permits: $50 - $200 (varies by location)
With careful planning and a little elbow grease, you can build a 12x20 storage shed on a budget that fits your needs and your wallet. Just remember to do your research, be patient, and most importantly, have fun! After all, that's what DIY is all about.
So, what are you waiting for? Get out there and start building!
Creating a beautiful garden shed: diy 10x12 plans

Hey there, fellow green thumbs! Tired of your tools cluttering the garage, and dreaming of a dedicated space for all your gardening goodies? Well, grab your favorite beverage, pull up a comfy chair, and let's talk about building your very own 10x12 garden shed!
This isn't some intimidating, "professional-only" project. Nope, this is a DIY adventure that's totally doable for anyone with a bit of elbow grease and a dash of determination. We'll walk through it step-by-step, making sure you feel confident and empowered to create a space that's as beautiful as it is functional.
The 10x12 Blueprint: Starting with the Basics
So, we're going with a 10x12 footprint. This gives you a good amount of space for tools, supplies, and even maybe a little potting bench or a cozy nook for enjoying your morning coffee while admiring your garden. Before we dive into the details, let's talk about a few important things:
Materials: We'll be working with pressure-treated lumber for the foundation and floor, and regular lumber for the walls and roof. Consider investing in high-quality wood to ensure your shed lasts for years.
Tools: You'll need the standard woodworking arsenal: a saw, drill, measuring tape, level, hammer, nails, and screws. A circular saw, table saw, or miter saw will make cutting precise angles a breeze.
Foundation: We'll be building a simple, sturdy foundation using concrete blocks or pressure-treated skids. This will ensure your shed is level and won't sag over time.
Laying the Foundation: A Stable Start
Now, let's get those hands dirty! The foundation is the cornerstone of your shed, so take your time and make sure it's solid.
1. Choosing Your Foundation: Concrete blocks are a classic choice, providing a solid base. Pressure-treated skids are another option, offering a more flexible and potentially faster build.
2. Leveling and Positioning: Use a level and stakes to mark the exact dimensions of your shed on the ground. Make sure it's level and in a location that gets good drainage.
3. Setting Your Foundation: If using blocks, create a level bed of gravel and set the blocks in place, using mortar for extra stability. If using skids, ensure they are level and secured to the ground with concrete anchors or heavy-duty brackets.
Framing Up the Walls: Building a Strong Skeleton
With the foundation in place, let's get those walls standing tall! This is where you'll start to see your shed taking shape.
1. Cutting the Walls: Measure and cut your wall studs to the correct height, using your saw. Remember to account for the thickness of your siding and any trim you'll be using.
2. Building the Wall Frames: Lay the studs flat on the ground, spaced 16 inches apart, and attach them to the top and bottom plates using nails or screws. You can also add diagonal braces for extra strength.
3. Raising the Walls: Carefully lift the wall frames into place, making sure they're plumb and aligned with the foundation. Temporarily brace the walls in place until they're securely fastened.
4. Connecting the Walls: Once all the walls are up, use corner posts or brackets to join them together. Make sure the corners are square and level.
Roofing the Shed: A Shelter from the Elements
Now, let's give your shed a roof over its head! This is the part where you'll start to feel a sense of accomplishment.
1. Rafter Installation: Measure and cut the rafters to the correct length, considering the slope you want for your roof. Attach them to the top plates of the walls, ensuring they're properly spaced.
2. Sheathing the Roof: Lay plywood or OSB sheathing over the rafters to create a solid surface for your roofing material. Make sure the sheets are overlapping for added strength.
3. Installing the Roofing: Choose your roofing material â" shingles, metal, or even a green roof. Follow the manufacturer's instructions for proper installation, ensuring a weatherproof and attractive roof.
Finishing Touches: Making it Your Own
Okay, we're almost there! Now comes the fun part: making your shed truly your own.
1. Siding and Trim: Choose your siding â" wood, vinyl, or metal â" and install it to the walls, adding trim around the windows and doors for a polished look.
2. Adding a Door and Windows: Measure and install your desired door and windows, ensuring they're securely fastened. Consider adding some decorative touches like a window box or shutters.
3. Painting or Staining: Bring out your creativity! Paint or stain the exterior of your shed in a color that complements your garden and home.
4. Adding the Finishing Touches: Install a simple workbench, shelves, and hooks for organizing your tools and supplies. Add some lighting for evening work sessions, and personalize the space to your liking.
Congratulations, You Did It!
And there you have it! You've just built a beautiful and functional 10x12 garden shed. Celebrate your achievement with a cup of tea and admire your handiwork.
This shed is more than just a storage space â" it's an extension of your garden, a haven for your tools, and a testament to your DIY skills. Now, get out there and enjoy all the possibilities your new shed offers!
Remember, if you find any part of the process daunting, don't hesitate to seek help from a more experienced DIYer or a local contractor. And, most importantly, have fun with the process! Building a shed is a rewarding experience that you'll cherish for years to come.
How to build a cheap 8x12 shed in no time

Alright, listen up, because I'm about to spill the secrets of building a cheap, awesome 8x12 shed in a way that'll make you think, "Man, I could totally do that!" We're not talking about some flimsy, rickety thing here. This is a sturdy shed that'll stand the test of time (and maybe a few neighborhood kids throwing rocks at it).
Let's start with the basics, shall we?
First, you need a plan. Not like a super detailed architect's blueprint, but more like a rough sketch on a napkin. You'll need to figure out where this shed is going to live in your backyard and if you need to get permits (check with your local building department - you don't want to end up with a shed that's illegal!).
Now, let's talk materials.
Think of it like a choose-your-own-adventure story, but for sheds.
Option 1: The classic wood frame.
This is the tried-and-true method, and it's relatively inexpensive. You'll need pressure-treated lumber for the foundation and floor, and you can use standard framing lumber for the walls and roof. Remember, pressure-treated lumber is your friend when it comes to keeping things dry and preventing rot.
Option 2: The metal siding showdown.
Metal siding is super easy to work with and stands up to the elements like a champ. Plus, it's cheaper than traditional wood siding. You can find metal siding kits at most home improvement stores, making it a super convenient choice.
Option 3: The DIY-er's dream (or nightmare, depending on your skill level).
You could always go the DIY route and build a shed entirely from scratch. This might sound intimidating, but it can be very rewarding (and definitely cost-effective). You'll need some serious woodworking skills, but if you're up for the challenge, you can build a truly unique shed that reflects your personality.
Now, let's talk tools. You'll need a few essentials:
A circular saw: This is your go-to tool for cutting lumber.
A drill: You'll need this for attaching everything together.
A tape measure: Precision is key here, so don't forget your trusty tape measure!
A level: A level ensures your shed is actually level, which is crucial for stability and aesthetics.
A hammer: You'll need this for hammering in nails and securing the roof.
Now, let's get down to business. It's time to build!
Step 1: The foundation.
This is the base of your shed, so you want to make sure it's strong. For a simple 8x12 shed, you can use pressure-treated 4x4s for the foundation posts. You'll want to dig holes about 3 feet deep and set the posts in concrete. Make sure the posts are level before you pour the concrete.
Step 2: The floor.
Now you're building the floor! You'll start by framing the floor with 2x6 or 2x8 lumber. Make sure you use pressure-treated lumber for the floor joists to prevent rot.
Step 3: The walls.
This is where you start seeing your shed really take shape. You'll build the walls using 2x4 framing lumber, and you can add insulation if you want a more climate-controlled shed.
Step 4: The roof.
Now it's time to add some shingles and make it weather-proof. You'll build the roof frame using 2x4 lumber, and you'll need to decide whether you want a simple gable roof or a more complex roof design.
Step 5: The siding.
You'll be able to choose between wood or metal for your siding, but I'll let you decide! Metal siding will be easier to install, but wood siding has that classic shed charm.
Step 6: The door and windows.
Now you're putting the finishing touches on your shed! You can choose a pre-made shed door from a home improvement store or build your own. Windows are also a good idea if you want natural light.
Step 7: The finishing touches.
Time for some fun! Paint your shed, add some trim, and make it your own! This is your chance to express your creativity and make your shed stand out.
Now, remember, you can always simplify things or add your own personal touches.
For example:
If you're on a tight budget, you can skip the insulation or use cheaper materials.
If you're feeling creative, you can add a loft or build some shelves inside.
You can also add a window or a door on the side of your shed for more light or access.
The beauty of building a shed is that you can make it exactly what you want it to be. It's your little piece of paradise in your backyard. And remember, the best thing about building a shed is that it's a project you can do yourself, step by step. It's a chance to learn something new, to create something tangible, and to have a lot of fun in the process.
So, what are you waiting for? Get out there and build your own shed! You'll be surprised at how easy it is and how much you'll enjoy the process. Plus, you'll have a fantastic new addition to your backyard that you can use for years to come. Happy building!
Build a cheap pole shed: design tips and cost-saving ideas

Alright, let's talk about building a pole barn. Maybe you're dreaming of a workshop to finally tackle those DIY projects, a storage space for your growing collection of "things," or maybe you just need somewhere to park your car out of the elements. Whatever the reason, a pole barn is a versatile and often surprisingly affordable option.
Now, before we dive into the nitty-gritty, let's get real - building a pole barn from scratch isn't a walk in the park. It takes some sweat equity, a little know-how, and maybe a few calls to your handy friend (we all have one). But, with some smart planning and a few cost-saving tips, you can build a pole barn that fits your budget and your needs.
First Things First: The Big Picture
What are you going to use it for? Knowing the purpose of your pole barn is crucial for planning. Do you need space for vehicles? Workshop tools? Hay storage? This will determine size, door placement, and even electrical needs.
Location, location, location! The site you choose will impact costs. Is it flat, requiring minimal grading? Is access easy for equipment delivery? Consider any local building codes or zoning requirements.
Think about the size. How much space do you REALLY need? It's easy to go overboard, but remember, more square footage means higher costs.
Let's Get Down to the Budget Basics
DIY or hire help? This is a biggie! If you're comfortable with construction, tackling most of the work yourself can save a lot of money. But, if you need help with specific tasks, don't hesitate to bring in professionals for those. It's all about finding the balance that works for you.
Materials Matter! Don't skimp on quality, but don't overspend either. Shop around for the best deals on lumber, concrete, and roofing materials. Consider using recycled or salvaged materials if possible, and don't be afraid to negotiate!
Consider the Extras. Things like insulation, windows, and siding can significantly increase costs. Think about what's truly essential and what you can do without initially. You can always add those features later.
Design Tips for a Budget-Friendly Barn
Keep it simple. A straightforward rectangular shape is often the most cost-effective. Avoid complex angles or intricate designs that require specialized materials or labor.
Standard sizes. Using standard sizes for lumber and building materials will help you get the best deals and reduce waste.
Go vertical. A taller pole barn can maximize space without requiring more square footage on the ground. This can save money on concrete and foundation costs.
Embrace open-air. For basic storage or vehicle protection, consider a partially open structure. It might not be climate-controlled, but it can save on roofing and siding costs.
Consider a lean-to. A smaller, attached structure can be a budget-friendly way to add storage space or shelter.
Cost-Saving Ideas to Stretch Your Dollar
Do your own foundation. While not for everyone, pouring your own concrete foundation can save you a significant chunk of change.
Get creative with materials. Consider using recycled materials for siding, roofing, or even flooring.
Go for a basic roof. A simple metal roof can be both durable and budget-friendly. Avoid complex roofing styles that require specialized installation.
Borrow or rent tools. Don't buy expensive tools for a one-time project. See if you can borrow them from friends, family, or rent them from a local tool rental company.
Leverage your skills. If you have carpentry skills, you can potentially save on labor costs by taking on more of the construction yourself.
Remember, building a pole barn is a journey, not a race! Take your time, plan carefully, and don't be afraid to ask for help. With a little effort and some creative cost-saving strategies, you can build a sturdy and functional pole barn without breaking the bank.
And don't forget, the satisfaction of building something with your own two hands is priceless!
Cost-effective materials for your diy 8x10 shed build
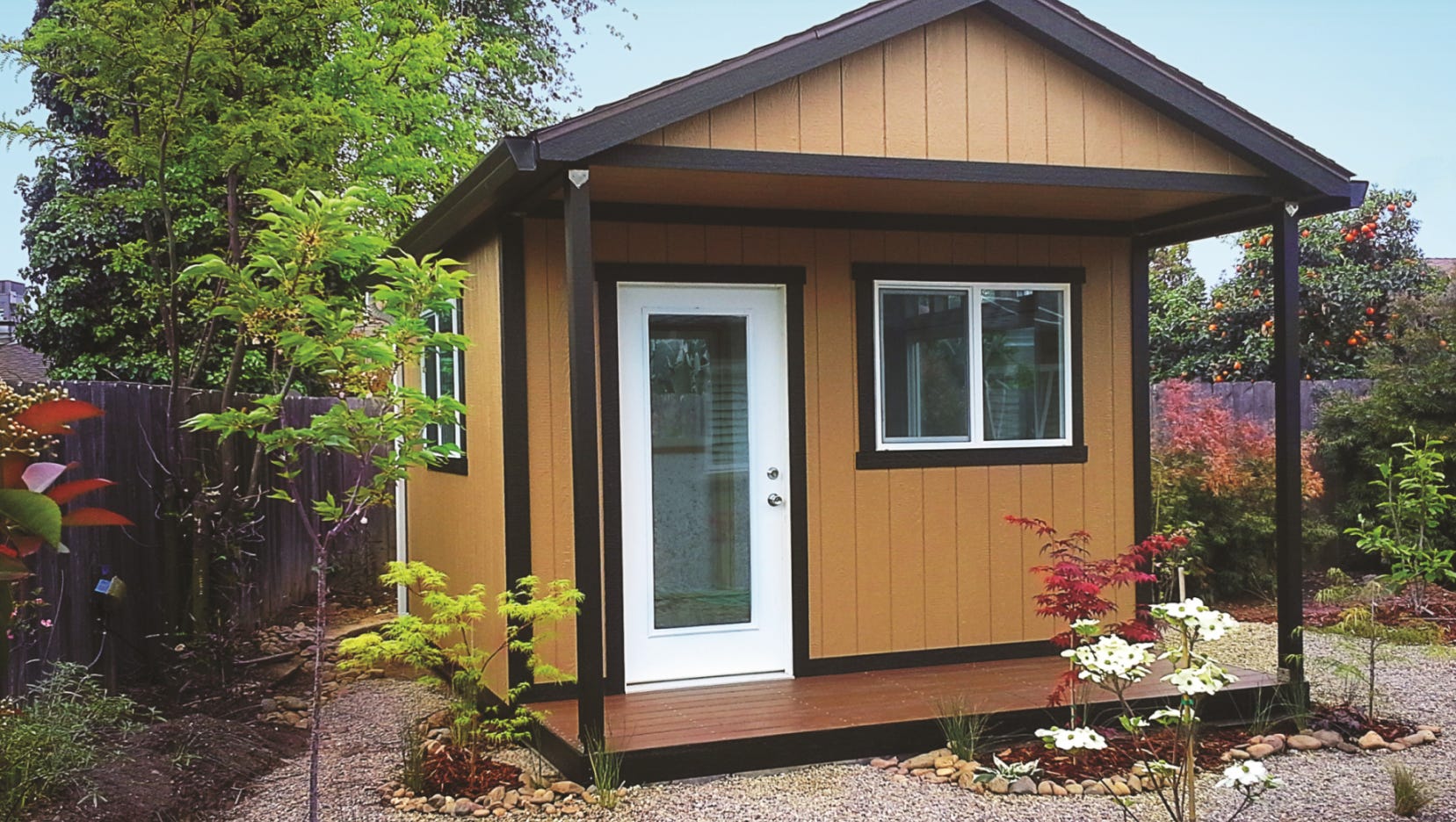
Alright, so you're thinking about building your own 8x10 shed, huh? That's awesome! It's a great way to add extra storage space to your property, and you can save a ton of money by doing it yourself. But let's talk about the cost-effective materials you'll need. I'm not talking about cutting corners, just making smart choices.
Foundation First: Forget the fancy concrete slab - unless you're building a palace, it's overkill. We're going for practicality. A gravel foundation is a great option. It's super affordable, and you can DIY it in a weekend. Here's the deal:
1. Level the ground: This is crucial for a stable shed. You don't want it tilting like a drunken pirate ship. Use a level and some sand to get it perfect.
2. Lay down landscape fabric: This stops weeds from popping up through your gravel and ruining your hard work.
3. Add a layer of gravel: About 4-6 inches should do the trick. Make sure to compact it well for a solid base.
The Walls: This is where you have some options. You can go with traditional wood framing, or you can get creative with pre-made panels.
Traditional Wood Framing: This is classic and gives you a lot of flexibility. Here's the breakdown:
Pressure-treated lumber for the base: This is essential to resist rot and keep your shed standing strong.
Standard 2x4s for the framing: This is what makes up the walls. Don't worry about fancy woods - spruce or pine will do the job just fine.
Plywood or OSB for sheathing: This goes on top of the framing to create a solid surface for the siding. Plywood is a little more expensive, but it's more stable and less prone to warping.
Siding: You can get away with inexpensive vinyl siding for a classic look. If you want something more rustic, cedar siding is a beautiful option, but it's more expensive.
Pre-Made Panels: This is a real time-saver and can be cheaper than traditional framing, especially if you're buying in bulk.
Look for "shed panels" or "wall panels": They come in various sizes and materials. They are basically pre-assembled walls that you just bolt together.
Make sure they are insulated: This will make your shed more comfortable to use year-round.
The Roof: Another important decision, and again, there are choices to make.
Traditional Shingle Roof: This is a classic choice and provides excellent protection from the elements.
Consider using asphalt shingles: They are affordable and easy to install.
Don't skimp on the underlayment: This layer goes under the shingles and protects your roof from leaks.
Make sure to get a good quality roof felt for underlayment: It's a small investment that will save you headaches in the long run.
Metal Roof: This is a more modern option that's becoming increasingly popular.
Metal roofs are durable and low maintenance: They can last for decades.
They can be more expensive than shingles: But you can find some decent deals on steel roofing panels.
The Floor: Your shed floor needs to be sturdy and easy to clean.
Simple and affordable: Consider using plywood or OSB for the floor.
Pre-treated plywood is ideal for this: It's more resistant to moisture and rot.
Lay down a moisture barrier: This will help prevent moisture from coming up through the floor.
Don't forget the details: Think about these things when you're planning your shed.
Windows: They let in light and can help ventilate your shed. You can find affordable window kits at most home improvement stores.
Door: Get a sturdy door with a good lock. Don't skimp on this - you want your belongings to be safe and secure.
Paint or stain: This protects your shed and gives it a finished look. Use a good quality paint or stain that's designed for outdoor use.
Finding the best deals: Here are some ways to save money on your shed materials:
Shop around: Compare prices at different lumberyards and home improvement stores.
Look for sales and clearance items: You can often find great deals on materials that are slightly damaged or have been discontinued.
Consider buying in bulk: If you need a lot of one type of material, like plywood or framing lumber, you can often get a discount by buying in bulk.
Ask about delivery costs: Some retailers offer free delivery, which can save you a lot of money on transportation.
Think about recycling and repurposing: You might be surprised what you can find in your garage or at a local recycling center. Old pallets, doors, or even windows can be repurposed for your shed.
Last but not least: Remember to plan out your project carefully and read the instructions thoroughly before you start building. There are tons of online resources and tutorials to help you with every step of the process. And don't be afraid to ask for help from friends or family if you need it. Building a shed is a great way to save money and create something useful for your home. Enjoy the process!
How to use storage shed plans for maximum efficiency

Okay, so you've got your storage shed plans, you've picked out the perfect location, and you're ready to build your own little haven for all your stuff. But wait! Before you grab that hammer and start swinging, take a minute to think about how you can make the most of your space. Building a shed is one thing, but building a shed that works like a well-oiled machine, that's an art form!
Let's dive into some tips and tricks for maximizing efficiency in your storage shed, making it the ultimate haven for your tools, lawn equipment, and all those "I'll need that someday" items:
1. The Power of Planning: Before You Even Start
Think of your shed plans as a blank canvas. Before you start painting, you need to figure out what you're going to put on it. This means taking inventory of all the things you want to store, considering their size, weight, and frequency of use. This will help you decide on the shed's size, layout, and features.
Here are a few things to consider:
What are you storing? This seems obvious, but knowing your stuff inside and out will help you plan the storage space effectively.
How often do you need to access these items? If you use something frequently, you'll want it to be easily accessible. Think about the flow of movement in your shed and how that affects the placement of items.
Do you need any special features? Need to store a motorcycle? How about a workbench for projects? Maybe you want an electrical outlet for powering tools. These are all things to incorporate into your plans.
2. Don't Fear the Vertical: Go Up, Up, Up!
The key to maximizing space in a shed is using every inch. Think vertically!
Shelving is your friend: Invest in adjustable shelving units. These allow you to customize the height of shelves to accommodate items of different sizes. And don't forget about the walls! You can install wall-mounted shelves to keep things off the floor and maximize floor space.
Overhead Storage: If you're dealing with bulky items or seasonal equipment, overhead storage can be a lifesaver. Consider a loft, pulley system, or even a simple raised platform to keep things out of the way but still within reach.
Utilize the Walls: Utilize pegboards or tool organizers to keep frequently used items easily accessible and within sight.
3. Organization is King (and Queen): Keeping Things in Their Place
A well-organized shed is a joy to use. Think about what you can do to make it easier to find and access your belongings.
Labeling is Key: Label everything! Use labels that are clear, concise, and easy to read. You can even use color coding for different categories.
Bins, Boxes, and Containers: Containers can be your best friend for storing smaller items, keeping them organized and dust-free. Use clear bins so you can see what's inside, and label them accordingly. You can even stack containers to save space.
Utilize Dividers: For drawers and cabinets, use dividers to create sections for different items. This keeps everything separated and easy to find.
4. Lighting Makes All the Difference
You've got your organization game on point, but you're still fumbling around in the dark? A well-lit shed is a safe and efficient shed!
Natural Lighting: Take advantage of natural light whenever possible by adding windows to your shed design.
Artificial Lighting: Invest in high-quality LED lights for even illumination. Consider adding motion sensor lights for easy access and security.
5. Think About Accessibility
Don't let your shed become a storage graveyard! Make sure you can easily get to everything you need.
Walkways and Paths: Make sure there's a clear walkway around the perimeter of your shed and a path to the door. This will prevent tripping hazards and make moving items in and out a breeze.
Think about Height: If you have items that are tall or heavy, consider adding a small platform or ladder to make it easier to access them.
6. Maintain and Clean Regularly
It's all too easy for a shed to become cluttered and messy over time. A little maintenance and cleaning can go a long way.
Regular Cleaning: Make it a habit to sweep, dust, and organize your shed regularly.
Pest Control: Keep your shed free of pests by using a pest control spray and sealing any cracks or holes.
7. Go Beyond the Basics: Adding Extra Features
Need to upgrade your storage game? Consider adding these extra features:
Workbenches: If you plan on using your shed for projects, a workbench is a must.
Electrical Outlets: Installing electrical outlets will power your tools and make your shed more functional.
Ventilation: Good ventilation is crucial for keeping your shed dry and preventing mold growth. Consider adding vents to your roof or walls.
Security Measures: Keep your belongings safe by installing a lock on the door and perhaps even an alarm system.
Building a shed is more than just throwing up some walls and a roof. By taking the time to plan and optimize your storage space, you can create a shed that's efficient, functional, and a true asset to your property. It's like having a mini-warehouse in your own backyard!
Saturday, November 9, 2024
How to design and build your 12x20 storage shed

Hey there, fellow DIY enthusiasts! Ever dreamt of a nice, organized space for all your tools, bikes, and maybe even a mini-workshop? A 12x20 storage shed is the perfect solution, offering ample space without being too overwhelming.
So, let's dive into the exciting journey of building your own shed! We'll cover everything from planning to finishing touches, making it a fun and rewarding project.
Phase 1: Planning and Preparation
1. Get Your Plans in Order:
Decide on a Location: Choose a spot that's easily accessible, level, and ideally near a power source if you plan on using electricity. Consider drainage, sun exposure, and any potential obstructions like trees or utility lines.
Design Your Dream Shed: Think about the size, shape, and features you want. Do you need a single door or double doors? Do you want windows for natural light?
Materials and Budget: Research different materials like wood, metal, or even recycled plastic. Set a realistic budget to ensure you're not overextending yourself.
Permits: Check your local building codes and obtain necessary permits for your shed construction.
2. Gather Your Tools:
Essential Tools: You'll need a saw (circular or miter), drill, hammer, tape measure, level, screwdriver, and safety gear like gloves, goggles, and ear protection.
Power Tools (Optional): If you're a seasoned builder, a power planer, router, and nail gun can speed up the process significantly.
3. Site Prep:
Clear the Area: Remove any vegetation, debris, and rocks.
Level the Ground: A flat surface is crucial for a stable shed. You might need to add or remove soil to achieve a level base.
Phase 2: Foundation and Framing
1. Building the Foundation:
Concrete Slab: The most durable option. You'll need a level, reinforced concrete slab poured and cured properly.
Concrete Blocks: More cost-effective than concrete, but require proper leveling and support.
Pressure-Treated Skirts: This is ideal for sheds placed directly on the ground. Ensure they're treated with preservative and well-secured.
2. Framing the Walls and Roof:
Framing Lumber: Choose high-quality pressure-treated lumber for the foundation, and standard lumber for the walls and roof.
Wall Framing: Cut and assemble wall frames according to your plans. Use corner braces and joist hangers for stability.
Roof Framing: Create rafters for your chosen roof type (gable, hip, or shed). Make sure they're well-supported and connected to the wall frames.
Phase 3: Sheathing and Roofing
1. Sheathing:
Plywood or OSB: Choose the right thickness based on your location's wind and snow load. Secure the sheathing to the framing with nails or screws.
2. Roofing:
Shingles, Metal, or Tile: Select a roofing material that complements your style and budget.
Underlayment: Install underlayment beneath the roofing material to protect against leaks.
Flashing: Use flashing around roof vents and at transitions to prevent water seepage.
Phase 4: Siding and Trim
1. Siding:
Vinyl, Wood, or Metal: Choose a siding material that suits your aesthetic and budget.
Install Siding: Follow the manufacturer's instructions for proper installation.
Soffits and Fascia: Install these decorative components to finish the roofline.
2. Trim:
Window and Door Trim: Add trim around windows and doors for a polished look.
Corner Trim: Protect corners and enhance the appearance.
Phase 5: Doors and Windows
1. Door Installation:
Pre-Hung Doors: These are easier to install and typically come with pre-installed hardware.
Installing Doors: Follow the manufacturer's instructions for proper installation and sealing.
2. Window Installation:
Pre-Hung Windows: These are easier to install, offering a clean look.
Installing Windows: Follow the manufacturer's instructions for proper installation and sealing.
Phase 6: Finishing Touches
1. Interior and Exterior Painting:
Prime and Paint: Prime the surfaces before applying paint for better adhesion.
Paint Color: Choose colors that complement your home and landscaping.
2. Insulation and Ventilation:
Insulation: Add insulation in the walls and ceiling for better temperature regulation.
Ventilation: Install vents in the roof and walls for proper air circulation.
3. Electrical Wiring:
Wiring: If you plan on using electricity in your shed, ensure all wiring is properly installed and meets local codes.
4. Flooring:
Concrete, Wood, or Tile: Choose a flooring material that suits your needs and budget.
5. Additional Features:
Shelving: Install shelves for storage.
Workbenches: Build a workbench for your tools.
Lighting: Install adequate lighting for working and visibility.
Phase 7: Enjoy Your New Shed!
Once your shed is complete, take a step back and admire your handiwork! You've created a valuable space for your belongings, and the satisfaction of building it yourself is priceless.
Remember:
Safety First: Always prioritize safety and use proper protective gear.
Double-Check: Measure twice, cut once! Avoid mistakes by carefully reviewing plans and measurements.
Seek Help When Needed: Don't be afraid to ask for help from family, friends, or professionals if needed.
Building your own 12x20 storage shed is a fantastic way to enhance your property and gain valuable skills. So, grab your tools, put on your work gloves, and get ready for a rewarding DIY adventure!