Featured Posts
Friday, November 22, 2024
How to Build a Wood Pallet Shed: Easy Plans for a Stylish Outdoor Shed
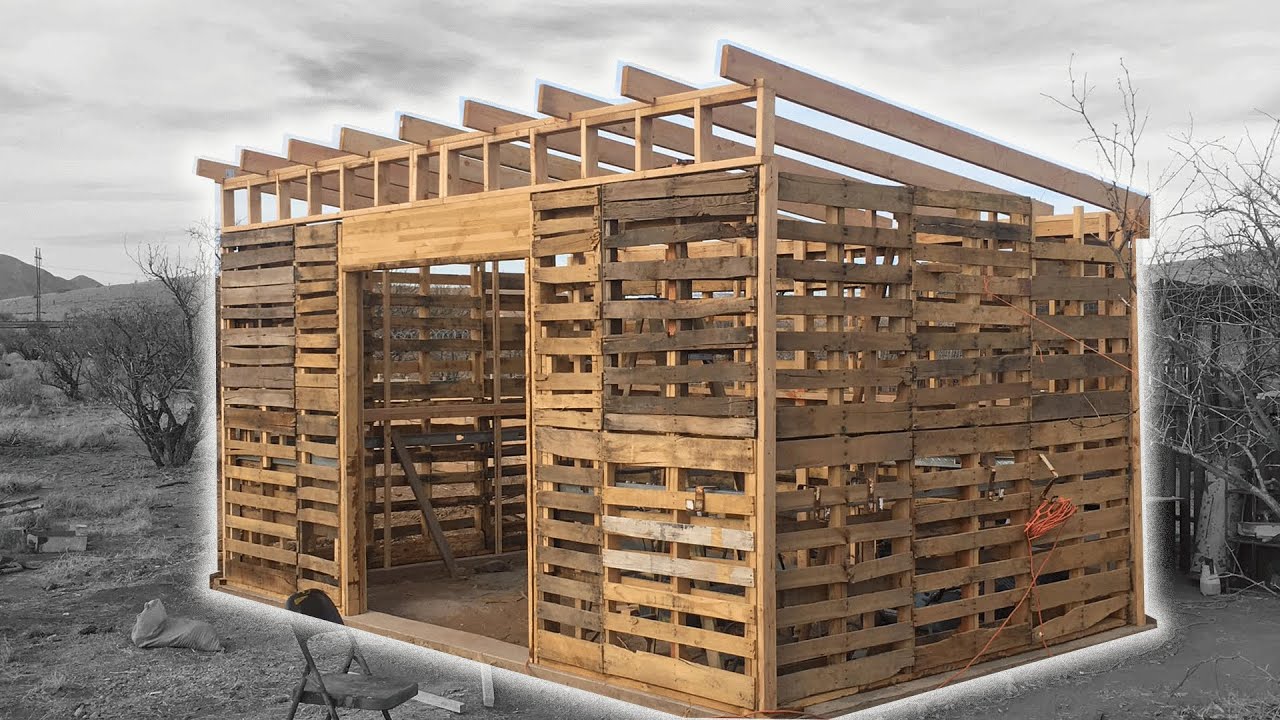
How to Build a Wood Pallet Shed: Easy Plans for a Stylish Outdoor Shed
Hey there, fellow DIY enthusiasts! So you're dreaming of a charming little shed, perfect for storing garden tools, bikes, or maybe even a cozy reading nook? And you're thinking of using reclaimed wood pallets? Fantastic! It's a super eco-friendly and budget-friendly option, plus you can get a really unique, rustic look. Let's dive into building your own pallet shed! Don't worry, even if you're a beginner, this project is totally doable.1. Planning Your Pallet Shed Paradise
Before you even think about grabbing a hammer, we need a plan. This isn't rocket science, but a little forethought saves a lot of headaches later on.1.1 Size and Location
First things first: how big do you want your shed to be? Consider what you'll be storing. A small shed for tools is different from a larger one that might house bikes and gardening supplies. Measure the space where you plan to place it, ensuring you have enough room to open doors and work comfortably. Also, think about sunlight â" do you need a sunny spot or a shadier area? Check local building codes for any restrictions on shed size or placement.
1.2 Pallet Selection: The Treasure Hunt
Now for the fun part â" sourcing your pallets! You can often find free or cheap pallets behind businesses, on Craigslist, or even Facebook Marketplace. Important note: Inspect them carefully! Make sure they're sturdy, free of rot, and haven't been treated with harmful chemicals. Look for the HT stamp (heat-treated) â" it means they're safe to use. You'll need quite a few, depending on the size of your shed, so start your hunt early.
1.3 Tools and Materials
Gather your arsenal! You'll need:
- Measuring tape and level
- Hammer or nail gun
- Screws (exterior-grade are best)
- Wood glue
- Saw (circular saw or hand saw)
- Safety glasses and work gloves
- Post hole diggers (if you plan on a concrete base)
- Concrete mix (optional, for a more stable base)
- Optional: Pressure treated lumber for the base framing if you are not using a concrete base
- Optional: Roofing felt and shingles
- Optional: Paint or stain for a finished look
Remember to always prioritize safety! Wear safety glasses and work gloves throughout the project.
2. Building the Foundation: A Solid Start
A sturdy foundation is key! You have a couple of options:
2.1 Concrete Base
This is the most permanent and robust option. Dig holes for your base supports, pour in concrete, and let it cure completely. Once set, you can attach your base framing to the concrete using anchors.
2.2 Wooden Base
A simpler approach is using pressure treated lumber to construct a frame. This creates a raised base and keeps the pallets off the ground, preventing rot. Ensure this base is level before continuing.
3. Constructing the Walls: Pallet Power!
This is where the pallet magic happens. Clean your pallets thoroughly, removing any loose nails or debris.
3.1 Wall Assembly
You can build walls either by stacking pallets directly or by creating a frame and attaching the pallets to it. For a more robust structure, using a frame is recommended. Build your frame using pressure-treated lumber and attach the pallets to this framework using screws. Consider using more than one pallet to build a taller wall section if needed. Work in sections until the walls are complete.
3.2 Securing the Walls
Once your walls are assembled, connect them using additional framing and screws to create a sturdy rectangular structure. Ensure the corners are square and properly aligned. You might want to use bracing inside the structure to add extra support.
4. Roofing the Shed: Shelter from the Storm
Now for the roof! There are several options here, depending on your skill level and desired aesthetic:
4.1 Simple Shed Roof
A single-sloped roof is easiest to build. You'll need to cut some pallets to the right size and angle for the roof and secure them to the top of your walls.
4.2 Gable Roof
A gable roof (with two slopes meeting at a ridge) offers more headroom inside, but is slightly more complex to construct. You will need extra supports and more precise cuts for this option.
4.3 Roofing Material
Once the roof structure is complete, you can add roofing felt to make it waterproof and then add your shingles or other roofing material of choice. Remember to overlap the roofing material to ensure complete protection from the elements.
5. Finishing Touches: The Personalization Phase
This is where your creativity shines! You can:
- Paint or stain the pallets for a more polished look.
- Add a door (a repurposed door works wonders).
- Install windows for ventilation and light.
- Add some landscaping around your new shed to make it blend seamlessly into your garden.
Commonly Asked Questions
Q: How long does it take to build a pallet shed?
A: This depends on the size and complexity. Expect to spend several days to a couple of weeks, depending on your experience and how much time you can dedicate to the project.
Q: Are pallets always free?
A: Not always. While you can often find free pallets, some may charge a small fee. Be sure to inspect pallets for safety and structural integrity before using them.
Q: What kind of paint should I use on pallets?
A: Use exterior-grade paint designed to withstand the elements. Apply multiple coats for better protection.
Q: Do I need planning permission to build a shed?
A: It depends on your local regulations and the size of the shed. Check with your local council before starting your project.
Q: Can I use any type of pallet?
A: No, it's important to only use pallets marked "HT" (heat treated) as these are safe for use. Avoid using pallets treated with chemical pesticides, as these are unsafe and potentially dangerous.
There you have it! Building a pallet shed is a rewarding project that combines creativity, resourcefulness, and a touch of rustic charm. So get out there, find those pallets, and unleash your inner builder. Happy shedding!
Thursday, November 21, 2024
The Ultimate DIY Lean-To Shed: Step-by-Step Plans for Outdoor Bliss
The Ultimate DIY Lean-To Shed: Step-by-Step Plans for Outdoor Bliss
Tired of battling the elements while tending your garden or storing your outdoor equipment? A lean-to shed offers the perfect blend of practicality and aesthetic appeal, providing sheltered space without overwhelming your backyard. This comprehensive guide empowers you to build your own, transforming your outdoor area into a haven of organization and convenience. Forget overpriced, pre-fabricated sheds; embrace the rewarding experience of crafting a personalized structure tailored to your specific needs. Let's dive into this fulfilling DIY project!
Planning Your Perfect Lean-To Shed
Before you grab your tools, careful planning is crucial. Determine the shed's intended purpose. Will it house gardening supplies, bicycles, or serve as a workshop? This dictates the size and features you'll need. Consider your available space, ensuring the shed's dimensions complement your existing landscape without feeling cramped or imposing. Sketch a detailed plan, noting precise measurements for the walls, roof, and foundation. Factor in the location's sun exposure to optimize natural light and ventilation. Don't forget to check local building codes and obtain any necessary permits before breaking ground. This proactive approach ensures a smooth, legally compliant project.
Essential Materials & Tools
Gathering the right materials and tools is paramount for a successful build. You'll need pressure-treated lumber for durability, roofing materials (shingles, metal, or polycarbonate panels), concrete for the foundation (or alternative like gravel), screws, nails, and appropriate fasteners. Invest in quality tools such as a saw (circular saw or hand saw), drill, level, measuring tape, and safety glasses. A post hole digger will simplify foundation work. Prepare a comprehensive shopping list to avoid mid-project delays. Remember to purchase extra materials to account for potential errors or unforeseen needs.
Foundation & Framing: Building the Base
Begin by preparing the foundation. For a stable base, dig holes and pour concrete footings to support your vertical supports. Alternatively, use a gravel base for a less permanent solution. Next, erect the frame. Attach the vertical posts securely to the foundation, ensuring they are perfectly plumb. Use a level frequently to guarantee accuracy. Then, attach horizontal beams to create the wall frame. Precise measurements and strong bracing are key to a robust and long-lasting structure. Take your time; accuracy at this stage prevents problems later on.
Roof Construction: Protecting Your Investment
Roof construction requires careful attention to detail. Attach rafters to the top of the frame, ensuring they slope appropriately to facilitate water runoff. Use appropriate fasteners and reinforce connections for added strength. Install sheathing over the rafters to create a solid base for your roofing material. Finally, lay your chosen roofing material, following the manufacturer's instructions carefully. Remember, a well-constructed roof safeguards your shed's contents and prolongs its lifespan. Carefully inspect your work at each stage.
Finishing Touches: Adding the Personal Flair
Once the main structure is complete, add the finishing touches to personalize your lean-to shed. Consider adding a door for easy access. You can install simple shelving to maximize storage, or add a workbench if it's a workshop. Paint the exterior to blend with your surroundings or add a pop of color. Consider adding weather stripping around the door and windows for enhanced insulation and protection from the elements. These finishing touches transform your functional shed into a truly personalized space.
Safety First!
Throughout the entire process, prioritize safety. Always wear appropriate safety gear, including safety glasses, work gloves, and sturdy footwear. Use caution when operating power tools and follow the manufacturer's instructions carefully. Take breaks when needed to prevent fatigue and maintain focus. Working safely ensures a smooth project and prevents potential injuries.
Building your own lean-to shed is a rewarding experience that combines skill, creativity, and hard work. With careful planning and attention to detail, you'll create a valuable addition to your outdoor space, a testament to your DIY prowess, and a source of immense satisfaction for years to come.
Friday, November 15, 2024
12x20 Shed with Loft Blueprints: Detailed Designs for DIYers

12x20 Shed with Loft Blueprints: Detailed Designs for DIYers
This document provides comprehensive blueprints and design specifications for constructing a 12x20 foot shed with a loft. Intended for experienced DIYers, these plans detail the entire construction process, from foundation to finishing touches. Careful review and understanding of these plans are crucial before commencing construction. Improper execution may compromise structural integrity and safety.
I. Foundation and Site Preparation
A robust foundation is paramount for a long-lasting structure. The chosen foundation type will depend on several factors, including soil conditions and local building codes. Consult with a local building inspector to determine the appropriate foundation for your site.
A. Site Selection and Preparation
Select a level area with adequate drainage. Clear the area of vegetation, debris, and any obstacles. Mark out the 12x20 foot area precisely using stakes and string. Ensure accurate measurements are taken to avoid future complications.
B. Foundation Options
Several foundation options exist, each with its own advantages and disadvantages:
- Concrete Slab: Provides a strong, level base but requires significant excavation and concrete pouring. This is generally the most robust option.
- Gravel Base with Pressure-Treated Skids: A more cost-effective option, suitable for well-drained soil. Requires less excavation but may require more maintenance over time.
- Pier and Beam Foundation: Ideal for uneven terrain. Requires precise placement of piers and robust beam construction.
Note: Detailed specifications for each foundation type, including material quantities and construction techniques, are provided in the accompanying detailed blueprints.
II. Framing and Structure
The framing forms the skeletal structure of the shed and must be meticulously constructed to ensure stability and longevity. Pressure-treated lumber is recommended for all ground-contact components to resist rot and insect damage.
A. Floor Framing
The floor framing consists of pressure-treated sill plates, floor joists, and subflooring. Joists should be spaced appropriately (typically 16 inches on center) and securely fastened to the sill plates and to each other using appropriate fasteners. Engineered wood I-joists can be considered for longer spans to minimize deflection.
B. Wall Framing
Wall framing utilizes standard framing techniques. Construct wall panels on the ground for ease of assembly. Use appropriate sized lumber for studs (typically 2x4s or 2x6s) and ensure proper spacing and bracing. Install windows and doors during this stage.
C. Roof Framing
The roof framing can be either a gable or a shed roof. Detailed plans for both are provided. Rafters must be properly calculated to ensure adequate support for the roof load. Consider using ridge boards and purlins for added strength and stability. Properly slope the roof to facilitate water runoff.
D. Loft Framing
The loft framing necessitates additional support beams and joists. These must be securely connected to the main structure. Proper calculations for load-bearing capacity are crucial for safety. Consider using engineered lumber for the loft floor joists to minimize deflection and maximize load-bearing capacity.
III. Exterior Cladding and Roofing
The exterior cladding and roofing protect the shed from the elements. Choose materials that are durable, weather-resistant, and aesthetically pleasing. Adherence to local building codes regarding fire safety and wind resistance is essential.
A. Siding Options
Several siding options are available, each with its own advantages and disadvantages:
- Vinyl Siding: Low maintenance and relatively inexpensive, but can be damaged easily.
- Wood Siding: Classic look, but requires regular maintenance and painting.
- Metal Siding: Durable and weather-resistant, but can be more expensive.
B. Roofing Materials
Roofing materials should be chosen based on local climate conditions and budget:
- Asphalt Shingles: Cost-effective and widely available.
- Metal Roofing: Durable and long-lasting, but can be more expensive.
C. Installation
Detailed instructions for installing siding and roofing materials are provided in the accompanying blueprints. Proper flashing and sealing are crucial to prevent water leakage. Ensure all nails and screws are appropriately sized and driven to prevent damage to the materials.
IV. Interior Finishing and Loft Access
Interior finishing adds functionality and aesthetics to the shed. The loft access should be carefully planned and constructed to ensure safety and ease of use.
A. Interior Walls and Ceiling
The interior walls and ceiling can be finished with drywall, plywood, or other suitable materials. Consider insulation for added comfort and energy efficiency.
B. Loft Access
The loft access can be a fixed staircase or a retractable ladder. Choose the option that best suits your needs and the available space. Ensure that the access point meets safety regulations.
C. Electrical and Plumbing
If electrical or plumbing is required, ensure that all work is carried out by qualified professionals and meets all applicable codes. Proper grounding and safety measures must be implemented.
V. Safety Precautions
Safety is paramount throughout the construction process. Always wear appropriate safety gear, including safety glasses, gloves, and hearing protection. Follow all manufacturer's instructions for tools and materials. Obtain necessary permits before commencing construction and adhere to all local building codes.
This document provides a general overview. The accompanying detailed blueprints contain precise measurements, material lists, and step-by-step instructions. It is crucial to carefully study and understand these blueprints before initiating the construction of your 12x20 shed with loft. Any deviation from these plans could compromise structural integrity and safety.
Monday, November 11, 2024
How to Design a Pole Barn with Ample Storage for Seasonal Items
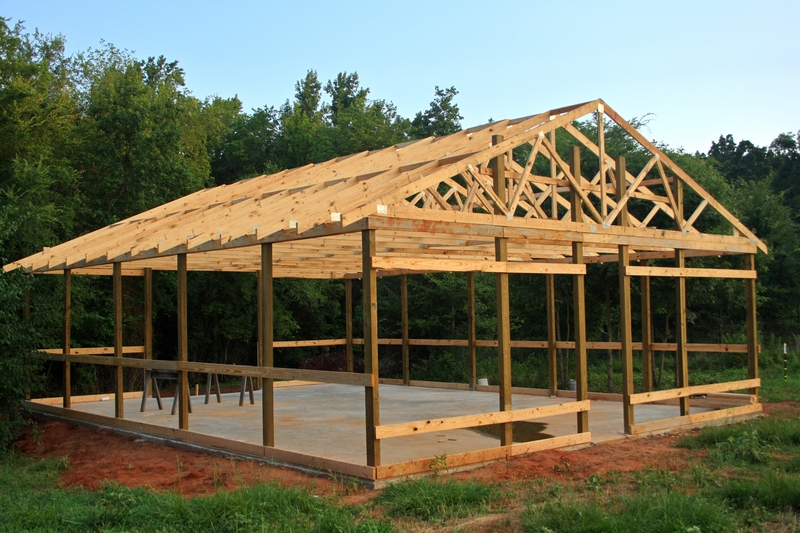
Okay, let's talk pole barns. You know, those sturdy, practical structures that have become synonymous with storage, workshops, and even living space. But we're going to focus on the storage part, specifically for all that seasonal stuff that takes over your garage or basement. Think kayaks, lawnmowers, holiday decorations, winter gear â" you name it, it's going to have a place in your new pole barn paradise.
Step 1: Dream Big, But Be Realistic
Before you start sketching out your perfect pole barn on a napkin (we've all been there!), let's get real. Think about the space you actually need. How much stuff are we talking about? Are you planning on storing vehicles, too?
Here's a little exercise to get you started:
List everything: Write down every single item you want to store in the barn.
Categorize: Group items into categories (e.g., lawn and garden, sports equipment, holiday décor, etc.)
Measure: Go through your list and actually measure the dimensions of each item. This is crucial for planning your layout.
Step 2: Planning the Layout â" It's All About Flow
Now that you know what you're working with, you can start to plan the layout. Imagine yourself moving through the barn â" where will you enter? Where will you store the most-used items? Where can you park a vehicle, if needed?
Think vertical: Utilize vertical space with shelves, racks, and even overhead storage systems. You'd be surprised how much you can store by going up!
Leave room to breathe: Don't cram everything in, leaving no room to move around. Allow for aisles and walkways for easy access.
Consider future needs: Will you need to add more storage in the future? Plan for expansion. Maybe have a small section designated for future additions.
Step 3: Choosing Your Pole Barn Materials â" The Basics
Pole barns are known for their durability and affordability. But there are a few things to consider when choosing materials:
Posts: Typically made of treated lumber, steel, or concrete. Treated lumber is cost-effective, while steel and concrete offer superior durability.
Roofing: Metal roofing is a popular choice due to its longevity and affordability. It also provides good insulation.
Siding: Vinyl siding is a good option for low maintenance, while metal siding is more durable.
Windows and Doors: Consider adding plenty of windows for natural light and ventilation. Choose a door size that allows you to easily move large items in and out.
Step 4: Beyond the Basics â" Adding Your Personal Touch
Your pole barn is going to be more than just storage; it's an extension of your home. Think about how you want to use the space and add some personal touches:
Work area: Designate a corner for a workbench, tools, and project supplies.
Lighting: Proper lighting is essential for working and safety. Consider LED lighting for energy efficiency.
Heating and cooling: If you plan to spend time in the barn, consider adding heating and cooling systems.
Flooring: Concrete floors are durable but can be cold. Consider adding a layer of epoxy or adding mats for comfort.
Step 5: The Finishing Touches â" Making it Your Own
Now for the fun part â" adding your personal flair to the space.
Wall colors: Choose a neutral color that reflects light, or add pops of color to define different areas.
Organization systems: Invest in storage solutions that fit your needs, such as shelves, bins, and hooks.
Decor: Add a few personal touches, like a vintage sign, a cozy armchair, or even a mini fridge for those long working days.
Here are some ideas for maximizing storage space:
Ceiling Storage: Install overhead storage systems for those items you don't use often, such as holiday decorations or seasonal clothing.
Vertical Storage Racks: Use wall-mounted racks for tools, sporting equipment, and even bikes.
Sliding Doors: Optimize space by installing sliding doors instead of traditional swing doors, especially if you have limited space.
Utilize the Walls: Use pegboards, shelves, and hooks to keep tools and accessories organized and easily accessible.
Go Up! Think about adding a loft for additional storage or even a workspace.
Don't forget the fun part! Remember, this is your space to enjoy. Add some personal touches, make it comfortable, and make it reflect your personality.
Building a pole barn is a great way to gain valuable storage space and add value to your property. By following these tips, you can create a functional and beautiful space that you'll love for years to come.
DIY Pole Barn Plans for Your Farm or Homestead
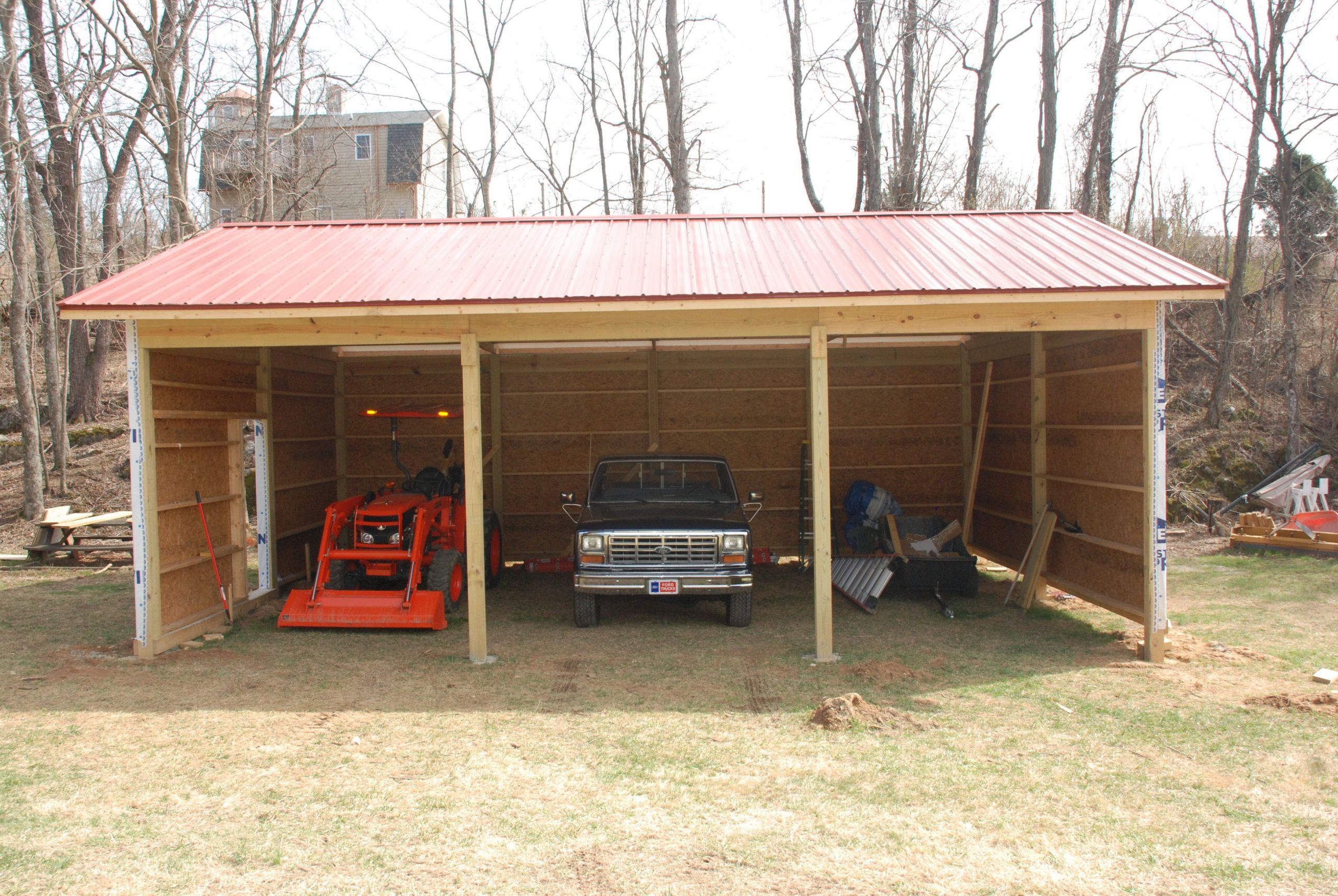
Hey there, fellow homesteaders! Ever dreamed of a big, beautiful pole barn to house all your tools, equipment, and maybe even a few furry friends? Building your own pole barn is a great way to get the space you need without breaking the bank. It's a project that might seem daunting at first, but trust me, it's way more doable than you think!
Why Choose a Pole Barn?
First things first, why are pole barns so darn popular with homesteaders? Let's break it down:
Cost-Effective: Compared to traditional stick-built structures, pole barns are budget-friendly. You're using less material, and the simplicity of the design means less labor.
Easy to Build: The basic construction is straightforward, making it a great project for DIYers with some experience.
Versatile: Pole barns are incredibly adaptable! Use them for storage, workshops, animal shelters, even living space with some creative planning.
Strong and Durable: Pole barns are built to last! The sturdy posts and open structure withstand heavy loads and the elements.
The Planning Stage: Getting Your Ducks in a Row
Before you grab your tools, it's essential to plan your project like a seasoned farmer! Here's what to think about:
1. Design and Size: What will you use the barn for? That'll determine your size and shape. Do you need a wide open space for equipment or a few stalls for horses?
2. Location, Location, Location: Consider the location of your barn on your property. Think about access, drainage, and proximity to existing utilities. A good rule of thumb is to make sure it's accessible by a truck or tractor.
3. Permits and Codes: Check with your local building department. They'll tell you about any specific requirements for pole barns in your area.
4. Budget and Materials: Do your research! Different types of wood and metal will affect your cost. Plan to factor in everything from lumber to concrete to roofing materials.
5. Tools and Equipment: You'll need a basic set of tools for construction, including a tape measure, level, circular saw, hammer, drill, and concrete mixer. You may also want to consider renting heavy equipment, like a post hole digger or a skid steer.
Getting Started: The Foundation of Your Barn
Now comes the fun part: building the foundation! Here's the basic process:
1. Preparing the Site: Clear the area, mark the location of the posts, and level the ground.
2. Digging the Holes: This is where your post hole digger or skid steer comes in handy! Dig holes for your support posts, making sure they're deep enough to be below the frost line.
3. Concrete Forms: If you're using concrete piers, create forms to hold the concrete in place.
4. Setting the Posts: Place the posts in the holes, making sure they're plumb and level. Secure them with temporary bracing.
5. Pouring Concrete: Once the forms are set, pour concrete into the holes to secure your posts. Let the concrete cure properly.
Framing the Barn: Raising the Roof
With your foundation secure, it's time to build the framework!
1. Setting the Ridge Beam: Place the ridge beam on top of the posts, securing it with metal brackets.
2. Installing Rafters: Cut and install the rafters, making sure they're properly spaced.
3. Sheathing the Roof: Attach plywood or OSB sheathing to the rafters to create a solid roof deck.
4. Installing Walls: Frame the walls using stud walls or prefabricated wall panels. Remember to allow for windows and doors!
Finishing Touches: Bringing Your Barn to Life
Once the basic framing is done, it's time to make your barn your own!
1. Roofing: Choose your roofing material based on your budget and style. Metal roofing is durable and popular for pole barns.
2. Siding: Siding options range from traditional wood to modern metal panels.
3. Windows and Doors: Add windows and doors for light, ventilation, and access.
4. Insulation and Finishing: If you plan on using the barn for living space or a workshop, add insulation to keep it comfortable. Finish the interior with drywall or other wall coverings.
A Little Bit of Advice:
Safety First: Always wear safety glasses and follow proper construction practices.
Don't Be Afraid to Ask for Help: There's no shame in enlisting help from friends, family, or professional contractors.
Enjoy the Process: Building your own pole barn is a rewarding experience! Take your time, celebrate your progress, and enjoy the fruits of your labor.
Building your own pole barn can be a lot of work, but it's also a rewarding experience! It's a chance to create a custom space that perfectly suits your needs, and it's a project you can be proud of for years to come.
Remember, this is just a basic overview. There are many different designs and techniques for building pole barns. Be sure to do your research and consult with a professional if needed. Happy building!
How to Design a Pole Barn for Your Specific Storage Needs

A pole barn, also known as a post-frame building, offers a versatile and cost-effective solution for a wide range of storage needs. Whether you require space for vehicles, equipment, livestock, or simply extra room for household items, a well-designed pole barn can serve as a practical and durable asset. This guide will provide a comprehensive overview of the design process, ensuring your pole barn meets your specific requirements.
1. Defining Your Needs and Goals:
Begin by meticulously outlining your storage needs. Consider the following:
Purpose: What will the pole barn primarily store? Vehicles, equipment, hay, livestock, or a combination?
Size: Determine the minimum square footage required to accommodate your belongings. Factor in aisle space for easy maneuverability.
Height: Ensure sufficient vertical clearance for vehicles, equipment, or potential future storage needs.
Doorways and Windows: Plan for appropriately sized doors for vehicle access, as well as potential windows for natural light and ventilation.
Flooring: Will the floor need to be concrete for heavy equipment or gravel for easier drainage?
Utilities: Do you require electricity, water, or other utilities?
Budget: Establish a realistic budget to guide design decisions.
2. Site Selection and Considerations:
Selecting the right site is crucial for optimal pole barn placement. Consider factors such as:
Accessibility: Ensure easy access for vehicles and deliveries.
Drainage: Choose a site with good drainage to prevent water accumulation around the building.
Zoning regulations: Confirm the site complies with local zoning ordinances related to building size, setbacks, and permitted uses.
Soil conditions: Investigate the soil type to determine if it's suitable for supporting the pole barn foundation.
Sun exposure: Evaluate the site's sun exposure for potential natural lighting and solar energy options.
Wind exposure: Consider the site's wind exposure, as it can affect the building's structural stability.
3. Design and Planning:
Once your needs are defined and the site selected, begin designing your pole barn:
Structural Integrity: Consult with a qualified engineer to ensure the building meets local building codes and withstands anticipated loads. Consider factors like snow load, wind load, and potential future additions.
Foundation Design: Select a foundation type suitable for the soil conditions and anticipated loads. Common options include concrete piers, helical piles, or a combination.
Framing and Construction: Pole barns typically utilize vertical posts, girders, and trusses. Choose materials like treated lumber or steel for longevity and durability.
Roofing and Siding: Select roofing and siding materials that align with your budget and aesthetic preferences. Consider options like metal roofing, vinyl siding, or composite materials.
Insulation: Evaluate insulation needs based on your climate and intended use. Insulation can improve energy efficiency and create a more comfortable environment.
Ventilation: Plan for adequate ventilation to ensure proper air circulation, prevent moisture build-up, and create a healthier storage environment.
4. Essential Considerations for Specific Storage Needs:
Vehicle Storage:
Driveway and Parking: Plan for a wide and accessible driveway to accommodate vehicle movement.
Door Height and Width: Ensure doors are large enough to accommodate the tallest vehicles.
Floor Strength: Choose a strong concrete floor capable of supporting the weight of vehicles.
Equipment Storage:
Overhead Clearance: Provide sufficient height for tall equipment, including hoists or forklifts.
Shelving and Storage Systems: Consider incorporating shelves, racks, or other storage systems to optimize space.
Electrical Outlets and Lighting: Ensure adequate electrical outlets and lighting for operating equipment.
Livestock Storage:
Ventilation and Climate Control: Ensure proper ventilation and temperature control for animal comfort.
Water and Feed Storage: Plan for convenient storage of water and feed for livestock.
Manure Management: Consider manure handling systems for efficient waste removal.
Household Storage:
Organization: Designate specific areas for different categories of belongings.
Shelving and Storage Solutions: Utilize shelves, cabinets, and drawers for organized storage.
Lighting and Security: Install adequate lighting and security systems for peace of mind.
5. Choosing a Contractor:
Select a reputable contractor experienced in pole barn construction. Request bids from multiple contractors, comparing pricing, experience, and references. Ensure the contractor is licensed, bonded, and insured.
6. Permitting and Inspections:
Obtain necessary permits and inspections from local authorities before beginning construction.
7. Final Touches and Maintenance:
Once construction is complete, consider adding finishing touches like landscaping, paint, or decorative accents. Implement a regular maintenance schedule to ensure the longevity of your pole barn.
Conclusion:
Designing a pole barn for your specific storage needs requires meticulous planning and attention to detail. By carefully considering factors like site selection, structural integrity, and specific storage requirements, you can create a functional, durable, and aesthetically pleasing building that will serve you for years to come. Remember to consult with qualified professionals throughout the process to ensure your pole barn meets local building codes and is tailored to your unique storage needs.
How to Build a Pole Barn with Heavy-Duty Floor Construction
Pole barns, known for their versatility and cost-effectiveness, provide a robust solution for a variety of uses, from agricultural storage to workshops and garages. However, the success of any pole barn hinges on a strong foundation, especially when dealing with heavy equipment or demanding usage. This article delves into the meticulous process of constructing a pole barn with heavy-duty floor construction, emphasizing durability and longevity.
1. Site Preparation and Planning
a. Site Selection and Soil Testing:
The first step involves selecting a suitable site with appropriate drainage and minimal soil movement. Conducting a soil test is crucial to understand the soil composition and bearing capacity. This information will inform the choice of foundation design, ensuring adequate support for the structure and the heavy-duty floor.
b. Site Clearing and Grading:
Once the site is chosen, it needs to be cleared of any vegetation, debris, and existing structures. Grading the site involves leveling the ground to achieve a uniform slope, ensuring proper drainage and preventing water accumulation.
c. Determining the Pole Barn's Size and Layout:
Define the desired dimensions of the pole barn, taking into account the intended use, equipment storage, and accessibility requirements. Create a detailed plan outlining the placement of doors, windows, and internal features.
2. Foundation Construction: Laying the Groundwork for Durability
a. Concrete Piers and Footing:
The foundation of a heavy-duty pole barn floor typically involves constructing concrete piers, which act as support points for the floor system. These piers are embedded in the ground and connected by a reinforced concrete footing.
b. Concrete Slab Design and Reinforcement:
The floor slab design should account for the anticipated loads and traffic patterns. Reinforcement bars are incorporated within the concrete slab to enhance its tensile strength and prevent cracking.
c. Grading and Compaction:
Prior to pouring the concrete, the prepared area must be graded and compacted thoroughly. This ensures a stable and level surface for the concrete slab, minimizing settling and unevenness.
3. Floor Construction: Building a Foundation for Strength
a. Insulation and Vapor Barrier:
Insulating the floor beneath the concrete slab helps to reduce heat loss and improve energy efficiency. A vapor barrier is installed to prevent moisture from penetrating the insulation and potentially causing damage to the floor.
b. Gravel Base:
A layer of gravel is laid over the compacted soil, providing a drainage layer and enhancing the load-bearing capacity of the floor. This base serves as a buffer between the concrete slab and the underlying soil.
c. Concrete Slab Placement and Finishing:
Once the gravel base is in place, the concrete slab is poured and finished. It is vital to ensure proper consolidation and vibration of the concrete to achieve optimal density and strength.
4. Pole Frame Construction: Creating a Stable Framework
a. Pole Placement and Erection:
The pole frame is erected directly onto the concrete piers, providing structural support for the roof and walls. The poles, typically made of treated lumber or steel, are spaced according to the design specifications.
b. Wall Construction and Bracing:
The walls are constructed using various materials such as wood framing, metal siding, or concrete blocks. Bracing is essential to ensure stability and prevent the walls from bowing or collapsing under load.
c. Roof Construction and Framing:
The roof frame, often constructed using trusses, is attached to the pole frame and supports the roofing material. The choice of roofing material depends on the intended use of the pole barn and local climate conditions.
5. Heavy-Duty Floor Considerations:
a. Floor Finish:
The choice of floor finish depends on the intended use of the pole barn. Options include concrete, epoxy coatings, rubberized flooring, or specialized flooring for heavy equipment.
b. Load Capacity and Traffic Patterns:
When planning the heavy-duty floor construction, carefully consider the anticipated loads and traffic patterns. The floor design should accommodate heavy equipment, forklift traffic, and other potential stresses.
c. Drainage and Ventilation:
Proper drainage and ventilation are essential to prevent moisture buildup and ensure a healthy environment within the pole barn. Incorporating drains and ventilation systems helps to control moisture and maintain air quality.
6. Finishing Touches: Enhancing Functionality and Aesthetics
a. Doors and Windows:
Installing durable doors and windows ensures accessibility and provides natural lighting. The size and placement of doors and windows should align with the intended use of the pole barn.
b. Electrical Wiring and Plumbing:
Electrical wiring and plumbing systems should be installed according to local codes and regulations. The placement and capacity of electrical outlets and plumbing fixtures should be considered based on the pole barn's intended purpose.
c. Interior and Exterior Finishes:
Finishing touches such as paint, siding, and insulation enhance the aesthetics and functionality of the pole barn. The choice of finishes should complement the overall design and intended use of the structure.
Conclusion
Constructing a pole barn with heavy-duty floor construction demands meticulous planning, careful execution, and adherence to building codes. The foundation, floor, and frame should be designed to withstand the anticipated loads and ensure long-term durability. By carefully following these steps, you can create a robust and reliable pole barn that meets your specific needs and stands the test of time. Remember, consulting with qualified professionals, such as architects, engineers, and contractors, is crucial for ensuring a successful and safe construction project.